Organic silicon modified bi-component solvent-based polyurethane anti-corrosive coating and preparation method thereof
A technology of anti-corrosion coating and modified polyester, which is applied in the direction of polyurea/polyurethane coating, anti-corrosion coating, coating, etc., can solve the problems of high cost, anti-corrosion failure of chimneys, etc., and achieve the reduction of internal stress, easy anti-corrosion construction, high solid The effect of content
- Summary
- Abstract
- Description
- Claims
- Application Information
AI Technical Summary
Problems solved by technology
Method used
Image
Examples
Embodiment 1
[0038] a. Preparation of organosilicon oligomer: the raw materials of each composition are calculated by mass percentage: 60% of silane coupling agent, 10% of deionized water, and 30% of absolute ethanol.
[0039] Add 60% silane coupling agent and 15% absolute ethanol to the three-necked flask, and after the temperature rises to 70°C, add a mixed solution of 10% deionized water and 15% absolute ethanol dropwise, and control the dropping speed within half an hour finished adding. After continuing the reaction for 3 hours, the reaction was stopped. Then distill at normal pressure, and stop the distillation after the temperature of the remaining liquid in the bottle rises to 125°C. Silicone oligomers were prepared.
[0040] b. Preparation of organosilicon-modified polyester polyol: the raw materials of each composition are calculated by mass percentage: 10% of organosilicon oligomer, 35% of polyester polyol, and 55% of mixed solvent.
Embodiment 2
[0047] a. Preparation of organosilicon oligomer: the raw materials for each composition are calculated by mass percentage: 65% of silane coupling agent, 5% of deionized water, and 30% of absolute ethanol.
[0048] Add 65% silane coupling agent and 20% absolute ethanol to the three-necked flask. After the temperature rises to 60°C, add a mixed solution of 5% deionized water and 10% absolute ethanol dropwise, and control the dropping speed within half an hour. finished adding. The reaction was continued for 4 hours, and the reaction was stopped. Then distill at normal pressure, and stop the distillation after the temperature of the remaining liquid in the bottle rises to 105°C. Silicone oligomers were prepared.
[0049] b. Preparation of organosilicon-modified polyester polyol: the raw materials of each composition are calculated by mass percentage: 13% of organosilicon oligomer, 37% of polyester polyol, and 50% of mixed solvent.
[0050] Add silicone oligomer, polyester poly...
Embodiment 3
[0056] a. Preparation of organosilicon oligomer: the raw materials for each composition are calculated by mass percentage: 40% of silane coupling agent, 15% of deionized water, and 45% of absolute ethanol.
[0057] Add 40% silane coupling agent and 20% absolute ethanol to the three-necked flask. After the temperature rises to 63°C, add a mixed solution of 15% deionized water and 25% absolute ethanol dropwise, and control the dropping speed within half an hour. finished adding. After continuing the reaction for 3 hours, the reaction was stopped. Then distill at normal pressure, and stop the distillation after the temperature of the remaining liquid in the bottle rises to 110°C. Silicone oligomers were prepared.
[0058] b. Preparation of organosilicon-modified polyester polyol: the raw materials of each composition are calculated by mass percentage: 15% of organosilicon oligomer, 35% of polyester polyol, and 50% of mixed solvent.
[0059] Add silicone oligomer, polyester pol...
PUM
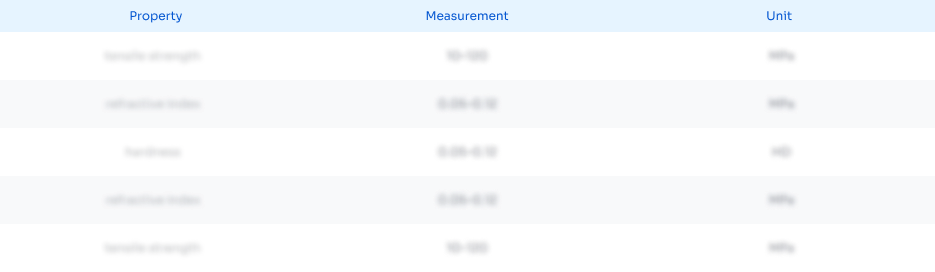
Abstract
Description
Claims
Application Information

- R&D Engineer
- R&D Manager
- IP Professional
- Industry Leading Data Capabilities
- Powerful AI technology
- Patent DNA Extraction
Browse by: Latest US Patents, China's latest patents, Technical Efficacy Thesaurus, Application Domain, Technology Topic, Popular Technical Reports.
© 2024 PatSnap. All rights reserved.Legal|Privacy policy|Modern Slavery Act Transparency Statement|Sitemap|About US| Contact US: help@patsnap.com