Method for producing ferronickel alloy grain by directly reducing lateritic nickel ore by rotary kiln
A nickel-iron alloy and laterite nickel ore technology, applied in the field of metallurgy and chemical industry, can solve the problems of high smelting grade requirements, complex process paths, environmental pollution, etc. Effect
Inactive Publication Date: 2011-06-15
徐伟
View PDF7 Cites 16 Cited by
- Summary
- Abstract
- Description
- Claims
- Application Information
AI Technical Summary
Problems solved by technology
Nickel is an important non-ferrous metal alloy element, mainly used for smelting stainless steel, nickel is used to produce stainless steel, nickel is a very large demand for stainless steel production enterprises, the usual production of nickel-based stainless steel needs to add 8wt-11wt% nickel, With the development of my country's stainless steel industry, the demand for nickel is increasing day by day, and the nickel resources that can be exploited and utilized by human beings are limited to two kinds of nickel sulfide ore and nickel oxide ore, of which 30% are nickel sulfide ore and 70% are nickel sulfide ore. % is nickel oxide ore. At present, there are three methods for producing ferronickel from laterite nickel ore, fire method, wet method, fire and wet combination method. Although the three methods can smelt ferronickel, there are different deficiencies. The disadvantage is that the former is difficult to popularize due to the high requirement of ore smelting grade, while the latter has complex process path, long process, high energy consumption, and serious environmental pollution, and it is also very unrealistic to use shaking table for gravity separation. Although the development of ferronickel is currently Research is very active, but has not yet seen a better solution to the above existing problems
Method used
the structure of the environmentally friendly knitted fabric provided by the present invention; figure 2 Flow chart of the yarn wrapping machine for environmentally friendly knitted fabrics and storage devices; image 3 Is the parameter map of the yarn covering machine
View moreExamples
Experimental program
Comparison scheme
Effect test
Embodiment 1
Embodiment 2
Embodiment 3
the structure of the environmentally friendly knitted fabric provided by the present invention; figure 2 Flow chart of the yarn wrapping machine for environmentally friendly knitted fabrics and storage devices; image 3 Is the parameter map of the yarn covering machine
Login to View More PUM
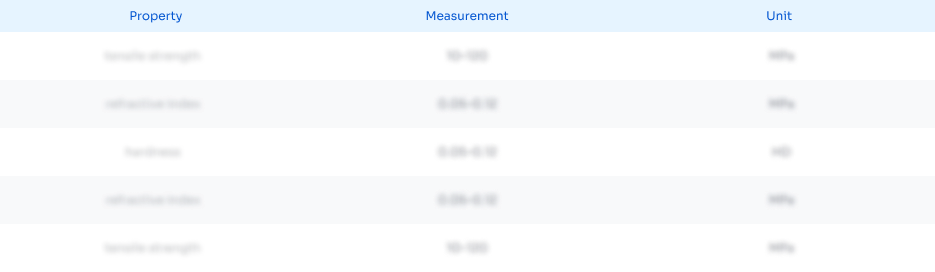
Abstract
The invention belongs to the technical field of metallurgical chemical industry and particularly relates to a method for producing ferronickel alloy grain by directly reducing lateritic nickel ore by a rotary kiln, comprising the following steps of: breaking and grinding the raw lateritic nickel ore free from drying; adding carbonaceous reducing agent and complex additive; removing natural moisture by a ball-pressing preheater; directly reducing in the rotary kiln; carrying out quenching and ore grinding to produced material; carrying out high-intensity magnetic separation to obtain the ferronickel alloy grain; and desulphurizing by using shell powder of which the activity is 40 times of that of the common lime stone. The ferronickel alloy grain contains less than 0.03% of sulphur, coal consumption of the method is 20% of that of the traditional process, The nickel recovery rate is more than 95%, the ferrum recovery rate is 70%, the tailing contains less than 0.08% of nickel, the reduction time is shortened, and the cost of the method is 1 / 3 of that of the traditional process. The tail gas of the rotary kiln can be used for generating electricity, the operation is simple and is easy to control, and the product is smelted by an electric furnace to directly smelt the ferronickel alloy grain; the quality of the product is good; a new path is provided for producing the ferronickel alloy grain; and the problems of high ore smelting grade, complex process, long flow, high energy consumption and environmental pollution can be solved.
Description
A method for directly reducing laterite nickel ore in a rotary kiln to produce nickel-iron alloy grains Technical field: The invention belongs to the technical field of metallurgy and chemical industry, and in particular relates to a method for producing nickel-iron alloy grains by directly reducing laterite nickel ore in a rotary kiln. Background technique: Nickel is an important non-ferrous metal alloy element, mainly used for smelting stainless steel, nickel is used to produce stainless steel, nickel is a very large demand for stainless steel production enterprises, the usual production of nickel-based stainless steel needs to add 8wt-11wt% nickel, With the development of my country's stainless steel industry, the demand for nickel is increasing day by day, and the nickel resources that can be exploited and utilized by human beings are limited to two kinds of nickel sulfide ore and nickel oxide ore, of which 30% are nickel sulfide ore and 70% are nickel sulfide ore. % is ...
Claims
the structure of the environmentally friendly knitted fabric provided by the present invention; figure 2 Flow chart of the yarn wrapping machine for environmentally friendly knitted fabrics and storage devices; image 3 Is the parameter map of the yarn covering machine
Login to View More Application Information
Patent Timeline

Patent Type & Authority Applications(China)
IPC IPC(8): C21B11/06C22B1/24
Inventor 徐伟
Owner 徐伟
Who we serve
- R&D Engineer
- R&D Manager
- IP Professional
Why Patsnap Eureka
- Industry Leading Data Capabilities
- Powerful AI technology
- Patent DNA Extraction
Social media
Patsnap Eureka Blog
Learn More Browse by: Latest US Patents, China's latest patents, Technical Efficacy Thesaurus, Application Domain, Technology Topic, Popular Technical Reports.
© 2024 PatSnap. All rights reserved.Legal|Privacy policy|Modern Slavery Act Transparency Statement|Sitemap|About US| Contact US: help@patsnap.com