Technology for preparing propylene by utilizing by-products in refinery
A by-product, propylene technology, applied in the field of propylene production, can solve the problems of low propylene yield and low added value of chemical utilization, and achieve the effects of high propylene yield, increased chemical added value, and good technical effects
- Summary
- Abstract
- Description
- Claims
- Application Information
AI Technical Summary
Problems solved by technology
Method used
Image
Examples
Embodiment 1
[0042] according to figure 1 As shown, the composition (% by weight) of the refinery mixed C4 is: isobutane: 40, n-butane: 10, n-butene: 15, butene-2: 30, isobutene: 5. The ethylene content in the dry gas was 20% by volume. The ratio of dry gas to mixed carbon four in the feed is 3 (by volume). The reactor is a single stage, filled with two layers of catalysts. The catalyst of the first layer is Mo / Mg metal oxide, and the catalyst of the second layer is ZSM-5 molecular sieve. The reaction temperature is 400° C., and the reaction pressure is 0.3 MPa. C 2 - The proportion of fraction recycle is 100% by volume. Cycle C 4 The mixture accounts for the C contained in the reactor outlet product 4 The proportion of 80% (volume). Towers 1 to 3 and the propylene rectification tower are sieve tray towers.
[0043] Experiments have shown that the propylene product obtained in the present invention is 41.8% (by weight, for the olefin content in the raw material).
Embodiment 2
[0045] according to figure 1 As shown, the composition (% by weight) of the refinery mixed C4 is: isobutane: 40, n-butane: 10, n-butene: 15, butene-2: 30, isobutene: 5. The ethylene content in the dry gas was 20% by volume. The ratio of dry gas to mixed carbon four in the feed is 5 (by volume). The reactor has two sections, the catalyst loaded in the first section is W / Mg metal oxide, and the catalyst in the second layer is SAPO-11 molecular sieve. The reaction temperature is 500° C., and the reaction pressure is 0.15 MPa. C 2 - The proportion of fraction recycle is 85% by volume. Cycle C 4 The mixture accounts for the C contained in the reactor outlet product 4 The proportion of 67% (volume). Towers 1 to 3 and the propylene rectification tower are sieve tray towers.
[0046] Experiments have shown that the propylene product obtained in the present invention is 39.3% (by weight, for the olefin content in the raw material).
Embodiment 3
[0048] according to figure 1 As shown, the composition (% by weight) of the refinery mixed C4 is: isobutane: 40, n-butane: 10, n-butene: 15, butene-2: 30, isobutene: 5. The ethylene content in the dry gas was 20% by volume. The ratio of dry gas to mixed carbon four in the feed is 8 (by volume). The reactor has three sections, the catalyst loaded in the first section is W / Mo / Mg metal, and the catalyst in the second and third layers is ZSM-5 molecular sieve. The reaction temperature is 500° C., and the reaction pressure is 0.05 MPa. C 2 - The proportion of fraction recycle is 70% by volume. Cycle C 4 The mixture accounts for the C contained in the reactor outlet product 4 The proportion of 80% (volume). Towers 1 to 3 and the propylene rectification tower are sieve tray towers.
[0049] Experiments have shown that the propylene product obtained in the present invention is 43.1% (by weight, for the olefin content in the raw material).
PUM
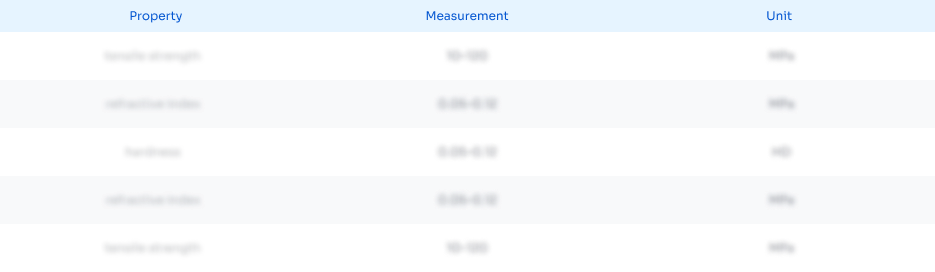
Abstract
Description
Claims
Application Information

- Generate Ideas
- Intellectual Property
- Life Sciences
- Materials
- Tech Scout
- Unparalleled Data Quality
- Higher Quality Content
- 60% Fewer Hallucinations
Browse by: Latest US Patents, China's latest patents, Technical Efficacy Thesaurus, Application Domain, Technology Topic, Popular Technical Reports.
© 2025 PatSnap. All rights reserved.Legal|Privacy policy|Modern Slavery Act Transparency Statement|Sitemap|About US| Contact US: help@patsnap.com