Preparation method of manganese-based MnAlSiTi alloy with high titanate content
A silicon-manganese alloy and alloy technology, applied in the field of manganese-based high-titanium content MnAlSiTi alloy and its preparation, can solve the problems of reduced alloying effect of composite deoxidizer, insignificant advantages of diversification of alloy elements, and pulverization of the overall structure of the alloy, etc. , to achieve the effects of easy polymerization, growth and exclusion, improvement of impurity removal rate, and stable alloy structure
- Summary
- Abstract
- Description
- Claims
- Application Information
AI Technical Summary
Problems solved by technology
Method used
Image
Examples
Embodiment 1
[0027] (1) Raw materials: 1000 kg of MnAlSiTi alloy is smelted, and the burning loss of raw materials is considered as 3%. The ratio is: 5 kg of scrap aluminum scraps, 150 kg of pure aluminum, 220 kg of ferro-titanium, and 655 kg of FeMn64Si16 alloy; the weight of the slagging agent is 10% by weight of raw materials, calcium oxide 75kg, silicon oxide 25kg, calcium fluoride 3kg, slag alkalinity 3.
[0028] (2) Raw material smelting:
[0029] A: Add slagging agent to the bottom of the smelting furnace, and add 10% of the raw material scrap aluminum;
[0030] B: After the waste aluminum chips added in step A are completely melted, add ferro-titanium, silicon-manganese alloy and the remaining waste aluminum chips;
[0031] C: After the ferrotitanium, silicomanganese alloy and remaining waste aluminum chips added in step B are completely melted, add pure aluminum block;
[0032] D: After the added raw materials are fully smelted, calm down for 3-5 minutes, remove slag, and pour i...
Embodiment 2
[0038] (1) Raw materials: 5000 kg of MnAlSiTi alloy is smelted, and the burning loss of raw materials is considered as 2%. The ratio is: scrap aluminum scrap 30 kg, pure aluminum 650 kg, titanium iron 1000 kg, FeMn68Si18 alloy 3420 kg; the weight of slagging agent is 5% by weight of raw materials, calcium oxide 135kg, magnesium oxide 50kg, silicon oxide 60kg, calcium fluoride 10kg, slag basicity 3.1.
[0039] Other steps are as described in Example 1.
[0040] The mass percentages of the components in the MnAlSiTi alloy prepared in this example are: Mn: 46.0%, Al: 14.3%, Si: 14.2%, Ti: 5.7%, and the rest are Fe and impurities.
Embodiment 3
[0042] (1) Raw materials: smelting 20,000 kg of MnAlSiTi alloy, the burning loss of raw materials is considered as 1%, and the ratio is: 200 kg of waste aluminum scraps, 2,000 kg of pure aluminum, 2,000 kg of ferrotitanium, and 16,000 kg of FeMn67Si23 alloy; the weight of slagging agent is 3% by weight of raw materials, calcium oxide 350kg, magnesium oxide 100kg, silicon oxide 120kg, calcium fluoride 36kg, slag alkalinity 3.75.
[0043] Other steps are as described in Example 1.
[0044] The mass percentages of the components in the MnAlSiTi alloy prepared in this example are: Mn: 53.3%, Al: 12.0%, Si: 16.2%, Ti: 3.0%, and the rest are Fe and impurities.
[0045] The yield of aluminum, manganese and titanium in the manganese-based MnAlSiTi alloy with high titanium content produced by the method of the present invention is high, and it will not be pulverized even if it is stored for 6 months under natural conditions, thereby meeting the requirements of industrial applications a...
PUM
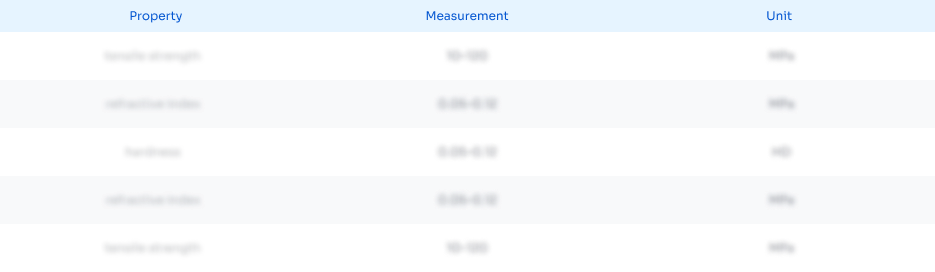
Abstract
Description
Claims
Application Information

- R&D
- Intellectual Property
- Life Sciences
- Materials
- Tech Scout
- Unparalleled Data Quality
- Higher Quality Content
- 60% Fewer Hallucinations
Browse by: Latest US Patents, China's latest patents, Technical Efficacy Thesaurus, Application Domain, Technology Topic, Popular Technical Reports.
© 2025 PatSnap. All rights reserved.Legal|Privacy policy|Modern Slavery Act Transparency Statement|Sitemap|About US| Contact US: help@patsnap.com