Preparation method of porous diatomite-based AgO ceramic material
A technology of ceramic materials and diatomite, which is applied in the field of preparation of diatomite-based porous AgO ceramic materials, can solve the problems of easy agglomeration of ultrafine AgO powder, high processing costs, and difficulty in recycling, and achieve low preparation costs and reduced sterilization cost, churn reduction effect
- Summary
- Abstract
- Description
- Claims
- Application Information
AI Technical Summary
Problems solved by technology
Method used
Image
Examples
preparation example Construction
[0017] The preparation method of the diatomite-based porous AgO ceramic material provided by the invention comprises the following steps:
[0018] Step 1: Clean the original diatomite with deionized water, then calcinate the cleaned diatomite at 540°C to 560°C for 2 hours, and cool down with the furnace to obtain refined diatomite;
[0019] Step 2, get the refined diatomite prepared in step 1 and mix it with glue to form a wet powder, the mass ratio of diatomite to glue is 2: 3, and the glue is composed of water, sodium carbonate, polyacrylamide and polyvinyl alcohol Composition, the mass ratio of water: sodium carbonate: polyacrylamide: polyvinyl alcohol is 1000: 67: 6: 4, the mixed wet powder is extruded into a sample, and the formed sample is dried at 60°C for 5h~7h, Calcining at 900°C for 0.5h, cooling in the furnace to obtain a porous ceramic sample, and making the ceramic sample into ceramic particles;
[0020] Step 3, immerse the ceramic particles prepared in step 2 in...
Embodiment 1
[0029] Wash the original diatomite with deionized water, calcinate at 540°C for 2 hours, and cool in the furnace to obtain refined diatomite; mix 10g of refined diatomite with 15mL of water, 1.0g of sodium carbonate, and 0.1g of polyacrylamide , 0.06g of polyvinyl alcohol was mixed evenly to prepare a molding wet powder, and the wet powder was extruded into a cylindrical sample with a diameter of 6 mm. After the molded sample was dried at 60°C for 5 hours, it was placed in a muffle furnace and heated at 900 Calcined at ℃ for 0.5h, cooled with the furnace to obtain a porous ceramic sample, and cut the ceramic sample into ceramic particles with a diameter of Φ×h of 6mm×6mm for later use; immerse 10g of diatomite-based ceramic particles in 25mL of silver nitrate with a concentration of 1.5mol / L In the solution, heat the silver nitrate solution containing ceramic particles to 40°C, and at a stirring speed of 2000r / min, add 100mL of potassium persulfate solution with a molar ratio o...
Embodiment 2
[0031] Wash the original diatomite with deionized water, calcinate at 550°C for 2 hours, and cool in the furnace to obtain refined diatomite; mix 10g of refined diatomite with 15mL of water, 1.0g of sodium carbonate, and 0.1g of polyacrylamide , 0.06g of polyvinyl alcohol was mixed evenly to prepare a molding wet powder, and the wet powder was extruded into a cylindrical sample with a diameter of 6 mm. After the molded sample was dried at 60°C for 6 hours, it was put into a muffle furnace and heated at 900 Calcined at ℃ for 0.5h, cooled in the furnace to obtain a porous ceramic sample, and cut the ceramic sample into ceramic particles with a diameter of Φ×h of 6mm×6mm for later use; immerse 10g of diatomite-based ceramic particles in 25mL of silver nitrate with a concentration of 2.0mol / L solution, then heat the silver nitrate solution containing ceramic particles to 60°C, and at a stirring speed of 2000r / min, add 100mL of potassium persulfate solution with a molar ratio of 3 t...
PUM
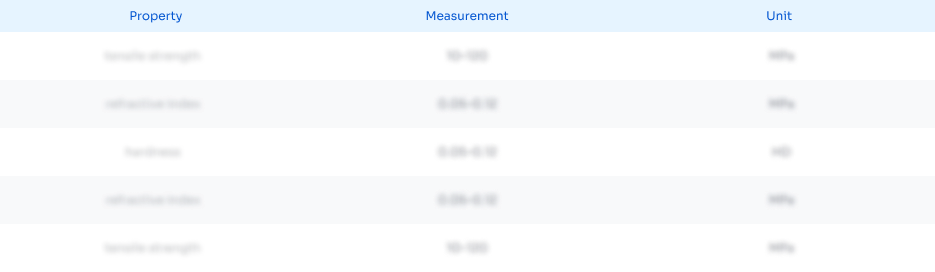
Abstract
Description
Claims
Application Information

- R&D Engineer
- R&D Manager
- IP Professional
- Industry Leading Data Capabilities
- Powerful AI technology
- Patent DNA Extraction
Browse by: Latest US Patents, China's latest patents, Technical Efficacy Thesaurus, Application Domain, Technology Topic, Popular Technical Reports.
© 2024 PatSnap. All rights reserved.Legal|Privacy policy|Modern Slavery Act Transparency Statement|Sitemap|About US| Contact US: help@patsnap.com