Tin-nickel-carbon alloy composite material for lithium ion battery and preparation method thereof
A technology of lithium-ion batteries and composite materials, which is applied in the field of tin-nickel-carbon alloy composite materials for lithium-ion batteries and its preparation, can solve the problems of powdered electrode performance of electrode materials, poor battery cycle performance, and deterioration, so as to improve the overall capacity , Improve the effect of cycle stability and life
- Summary
- Abstract
- Description
- Claims
- Application Information
AI Technical Summary
Problems solved by technology
Method used
Image
Examples
no. 1 approach
[0047] The tin-nickel-carbon alloy composite material for lithium-ion batteries is composed of 15% nickel powder, 20% tin powder, 58% graphite and 7% pitch, and the above percentages are all mass percentages.
[0048] The preparation method of the tin-nickel-carbon alloy composite material for lithium-ion batteries of the present embodiment is as follows:
[0049] (1) First mix 15% tin powder and 20% nickel powder according to the mass ratio and add appropriate amount of alcohol for high-energy mechanical ball milling for 10 hours;
[0050] (2) Then the alloy powder obtained by the above-mentioned mechanical ball milling was mixed with 58% graphite and alcohol was added to continue high-energy mechanical ball milling for 8 hours, and the particle size value of the added graphite was 15 μmm;
[0051] (3) Take out the above-mentioned tin-nickel alloy-carbon composite material to remove alcohol by suction filtration, then put it into an oven for vacuum drying for 8 hours, then ca...
no. 2 approach
[0055] The tin-nickel-carbon alloy composite material for lithium-ion batteries is composed of 20% nickel powder, 25% tin powder, 45% graphite and 10% pitch, and the above percentages are all mass percentages.
[0056] The preparation method of the tin-nickel-carbon alloy composite material for lithium-ion batteries of the present embodiment is as follows:
[0057] (1) First, mix 20% tin powder and 25% nickel powder according to the mass ratio and add an appropriate amount of alcohol for high-energy mechanical ball milling for 12 hours;
[0058](2) Then the alloy powder obtained by above-mentioned mechanical ball milling was mixed with 45% graphite and alcohol was added to continue high-energy mechanical ball milling for 10 hours, and the particle size value of the added graphite was 17 μm;
[0059] (3) Take out the above-mentioned tin-nickel alloy carbon composite material to remove alcohol by suction filtration, then put it into an oven for vacuum drying for 12 hours, then p...
no. 3 approach
[0063] The tin-nickel-carbon alloy composite material for lithium-ion batteries is composed of 25% nickel powder, 30% tin powder, 35% graphite and 10% pitch, and the above percentages are all mass percentages.
[0064] The preparation method of the tin-nickel-carbon alloy composite material for lithium-ion batteries of the present embodiment is as follows:
[0065] (1) First mix 25% tin powder and 30% nickel powder according to the mass ratio and add appropriate amount of alcohol for high-energy mechanical ball milling for 15 hours;
[0066] (2) Then the alloy powder obtained by the above-mentioned mechanical ball milling was mixed with 35% graphite and alcohol was added to continue the high-energy mechanical ball milling for 15 hours, and the particle diameter value of the added graphite was 18 μmm;
[0067] (3) Take out the above-mentioned tin-nickel alloy carbon composite material to remove alcohol by suction filtration, then put it into an oven for vacuum drying for 16 hou...
PUM
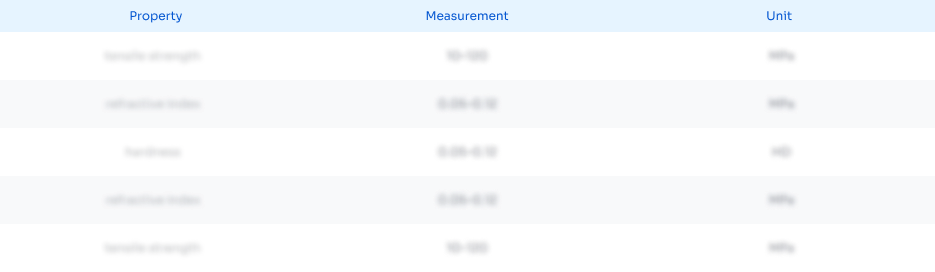
Abstract
Description
Claims
Application Information

- R&D Engineer
- R&D Manager
- IP Professional
- Industry Leading Data Capabilities
- Powerful AI technology
- Patent DNA Extraction
Browse by: Latest US Patents, China's latest patents, Technical Efficacy Thesaurus, Application Domain, Technology Topic, Popular Technical Reports.
© 2024 PatSnap. All rights reserved.Legal|Privacy policy|Modern Slavery Act Transparency Statement|Sitemap|About US| Contact US: help@patsnap.com