New production process of toughened vacuum glass
A vacuum glass and new process technology, applied in glass production, glass forming, glass tempering and other directions, can solve the problems of low production efficiency, low safety, low product qualification rate, etc., to improve production efficiency and automation level, The effect of expanding the scope of application and ensuring safety performance
- Summary
- Abstract
- Description
- Claims
- Application Information
AI Technical Summary
Problems solved by technology
Method used
Image
Examples
Embodiment Construction
[0026] See Figure 1 ~ Figure 4 , The present invention is a new process for the production of tempered vacuum glass, which is characterized by including the following process steps:
[0027] (1) Making a fulcrum: At least one flat glass surface is made to make a fulcrum 2, and the lead-free and cadmium-free high-temperature resistant glass glaze is uniformly dispersed and printed on the upper surface of the flat glass 7 below (see figure 1 , image 3 , Figure 4 ), forming a pivot 2.
[0028] (2) Curing: Dry the plate glass 7 that makes the pivot 2 naturally or send it into a drying oven for drying, (conventional process, natural drying for more than 1 hour, drying in a 120 ℃ oven for about 15 minutes) to form Design height and area pivot point 2.
[0029] (3) Tempering: Then it is sent to a continuous tempering furnace for tempering (conventional process) to make tempered glass 7 with fulcrum 2.
[0030] (4) Compounding and sealing: Place another piece of flat glass 4 drilled with ...
PUM
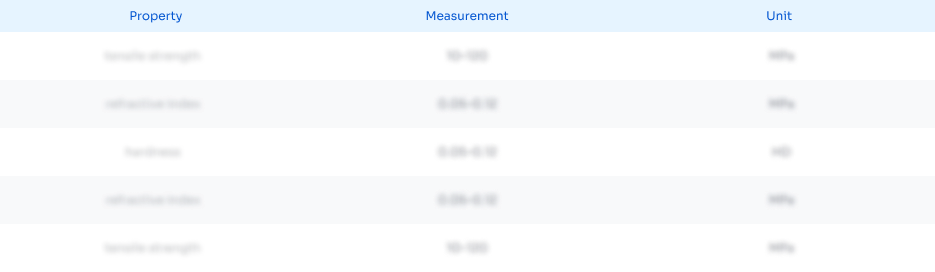
Abstract
Description
Claims
Application Information

- Generate Ideas
- Intellectual Property
- Life Sciences
- Materials
- Tech Scout
- Unparalleled Data Quality
- Higher Quality Content
- 60% Fewer Hallucinations
Browse by: Latest US Patents, China's latest patents, Technical Efficacy Thesaurus, Application Domain, Technology Topic, Popular Technical Reports.
© 2025 PatSnap. All rights reserved.Legal|Privacy policy|Modern Slavery Act Transparency Statement|Sitemap|About US| Contact US: help@patsnap.com