Deamination new process by alkaline hydrolysis of nitrile compounds
A compound and nitrile technology, which is applied in the field of alkaline deamination of nitrile compounds, can solve the problems of difficult recovery of ammonia condensation, high power consumption, high water consumption, and low concentration of ammonia water, so as to reduce equipment investment, improve recovery rate, and improve deamination The effect of ammonia efficiency
- Summary
- Abstract
- Description
- Claims
- Application Information
AI Technical Summary
Problems solved by technology
Method used
Image
Examples
Embodiment 1
[0021] 4180kg of aminoacetonitrile aqueous solution (containing 1120kg of aminoacetonitrile) was preheated to 60°C through a heat exchanger, and 1895L (specific gravity 1.32) of 32% liquid caustic soda was pumped into the rapid mixing alkaline hydrolysis reactor through a metering pump. The rapid mixing alkaline hydrolysis reactor produces amino acetic acid and releases ammonia during the reaction process. The reaction is an exothermic reaction. Under slight negative pressure, the ammonia produced by the reaction is carried away with water, and at the same time the heat generated by the reaction is taken away. The temperature of the hot water in the jacket is adjusted to maintain the temperature of the reaction material at about 75°C. , The residence time of each batch of aminoacetonitrile hydrolysate in the reactor is 35 minutes. After measuring in the measuring tank, 480L of ammonia water is produced every 35 minutes. The hydrolysis solution and ammonia water were sampled an...
Embodiment 2
[0026] 3960kg of anilinoacetonitrile aqueous solution (containing 1320kg of anilinoacetonitrile) is heated to 50°C and 1420L (specific gravity 1.32) 32% liquid caustic soda is pumped into the hydrolysis reactor through a metering pump respectively. During the reaction, sodium anilinoacetate is formed and ammonia is released. The reaction is exothermic. Under slight negative pressure, the ammonia produced by the reaction entrains water and is taken away, while taking away the heat generated by the reaction. The temperature of the jacketed hot water is adjusted to maintain the temperature of the reaction material at about 65°C. , The residence time of each batch of anilinoacetonitrile hydrolysate in the reactor is 30 minutes. After measuring by the measuring tank, 315L of ammonia water is produced every 30 minutes. The hydrolysis liquid and ammonia water were sampled and analyzed respectively. Among them, the specific gravity of the ammonia water was 0.92, the concentration was ...
Embodiment 3
[0031] Add 3000L of process water to the 5000L dissolving kettle, turn on steam to raise the temperature to 85°C, add 1630kg (15.78kmol) of 92% iminodiacetonitrile solid with stirring, and the temperature in the kettle will be 72°C after dissolution. After 3510L of 30% liquid caustic soda is measured by a metering pump, it and the dissolved iminodiacetonitrile solution are respectively pumped into the rapid mixing alkaline hydrolysis reactor through the metering pump. In the rapid mixing alkaline hydrolysis reactor, through efficient mass transfer and heat transfer, the iminodiacetonitrile and sodium hydroxide in the material fully contact and react, and at the same time release ammonia. The alkaline hydrolysis reaction is an exothermic reaction. Under slight negative pressure, the ammonia produced by the reaction is carried away with water, and at the same time the heat generated by the reaction is taken away. The reaction temperature is maintained at about 70℃. The reactor siz...
PUM
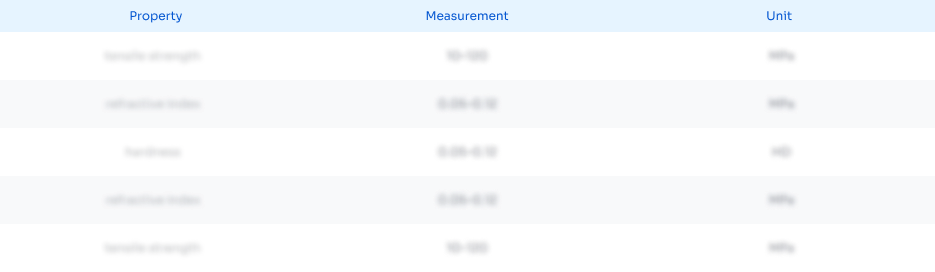
Abstract
Description
Claims
Application Information

- R&D
- Intellectual Property
- Life Sciences
- Materials
- Tech Scout
- Unparalleled Data Quality
- Higher Quality Content
- 60% Fewer Hallucinations
Browse by: Latest US Patents, China's latest patents, Technical Efficacy Thesaurus, Application Domain, Technology Topic, Popular Technical Reports.
© 2025 PatSnap. All rights reserved.Legal|Privacy policy|Modern Slavery Act Transparency Statement|Sitemap|About US| Contact US: help@patsnap.com