Method for manufacturing hollow box type element with non-circular section from carbon fiber composite
A composite material and a manufacturing method technology, which is applied in the field of manufacturing carbon fiber composite material non-circular cross-section hollow and complex shape box-shaped parts, can solve the problem that there is no relevant report on the manufacturing method, and achieve a simple and convenient processing method, and the mold manufacturing is simple and efficient. Inexpensive and time-consuming results
- Summary
- Abstract
- Description
- Claims
- Application Information
AI Technical Summary
Problems solved by technology
Method used
Image
Examples
Embodiment Construction
[0028] The rectangular part described in this embodiment is not the only special shape, but it can be considered that the present invention is applicable to various circular, rectangular cross-sections or cross-sections that vary along the member axis with angular, curved and twisted complex profiles and variable cross-sections. The processing technology of special-shaped cross-section hollow light-body components, special-shaped pipe fittings and non-circular cross-section hollow frames, frame beams and complex pipe fittings and other composite materials. The technical requirements of the mold are to be as light as possible, to ensure sufficient strength and rigidity, and to be disassembled conveniently and quickly.
[0029] In the accompanying drawings, according to the method of the present invention, the two sets of molds prepared are composed of upper and lower modules, connectors, fasteners, and seals, and no seals are provided between the well-matched modules. The abs...
PUM
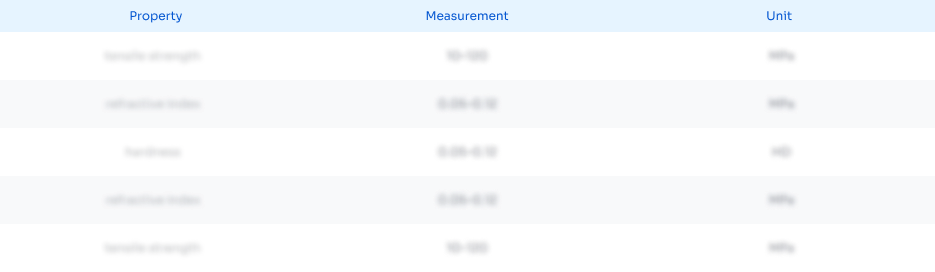
Abstract
Description
Claims
Application Information

- R&D
- Intellectual Property
- Life Sciences
- Materials
- Tech Scout
- Unparalleled Data Quality
- Higher Quality Content
- 60% Fewer Hallucinations
Browse by: Latest US Patents, China's latest patents, Technical Efficacy Thesaurus, Application Domain, Technology Topic, Popular Technical Reports.
© 2025 PatSnap. All rights reserved.Legal|Privacy policy|Modern Slavery Act Transparency Statement|Sitemap|About US| Contact US: help@patsnap.com