Self-adaptive casting mould manufacture method for casting
A manufacturing method and self-adaptive technology, applied in the fields of casting and CNC machining, can solve the problems of long core box processing cycle, unsuitable for large molds, and step effect, etc., to improve flexibility and operability, good casting performance, The effect of high processing flexibility
- Summary
- Abstract
- Description
- Claims
- Application Information
AI Technical Summary
Problems solved by technology
Method used
Image
Examples
Embodiment Construction
[0027] Attached below figure 1 , 2 The present invention is described in detail, but it is not intended to limit the present invention.
[0028] Specific steps are as follows:
[0029] (1) Use 3D software to establish a 3D solid model of the part, and deduce the mold cavity that needs to be cut according to the solid model;
[0030] (2) According to the performance requirements of the casting, the sand block structure design is carried out in blocks, and the number and size of a single sand block are determined; and the processing path is optimized;
[0031] (3) Preparation of a single sand block: For the hot spot or thick part of the casting, use zircon powder with a particle size of 50 / 100 mesh, binder, hardener, additives, etc. to make a sand block, or other heat-conducting materials can also be used Modeling materials with good coefficients such as graphite; for conventional parts, use quartz sand with a particle size of 70 / 140 mesh, binders, hardeners, additives, etc. ...
PUM
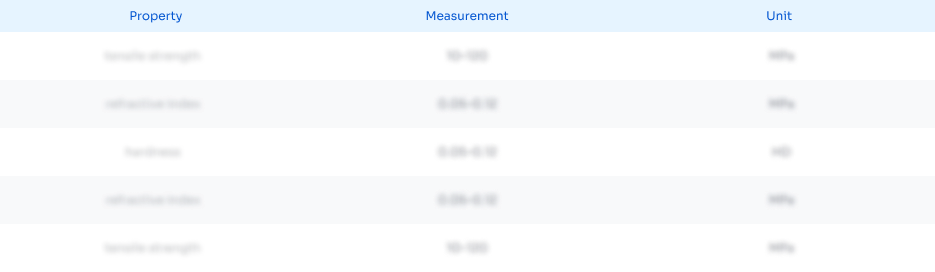
Abstract
Description
Claims
Application Information

- Generate Ideas
- Intellectual Property
- Life Sciences
- Materials
- Tech Scout
- Unparalleled Data Quality
- Higher Quality Content
- 60% Fewer Hallucinations
Browse by: Latest US Patents, China's latest patents, Technical Efficacy Thesaurus, Application Domain, Technology Topic, Popular Technical Reports.
© 2025 PatSnap. All rights reserved.Legal|Privacy policy|Modern Slavery Act Transparency Statement|Sitemap|About US| Contact US: help@patsnap.com