Method for preparing graphene-epoxy resin composite material
A technology of epoxy resin and composite materials, which is applied in the field of preparation of graphene-epoxy resin composite materials, can solve the problems of environmental pollution, complicated preparation methods, and few preparation methods, and achieve good monodispersity and simple operation process , the effect of controllable load
- Summary
- Abstract
- Description
- Claims
- Application Information
AI Technical Summary
Problems solved by technology
Method used
Image
Examples
Embodiment 1
[0010] Mix bisphenol A epoxy resin E51 and 0.3mg / mL graphene aqueous solution at a volume ratio of 1:0.5, control the temperature at 120°C, stir for 5 minutes, and stand still for 30 minutes to separate layers. Pour out the upper layer of aqueous solution, and the lower layer of graphite The alkene-epoxy resin continued to stir and react at 80°C for 12 hours, then added epoxy resin curing agent H-1618 (Shijiazhuang Huili Chemical Co., Ltd., Shijiazhuang, Hebei, China), and cured at 100°C for 1 hour, and then cured at 150°C After 2 hours, a cured graphene-epoxy composite material was obtained.
Embodiment 2
[0012] Bisphenol A epoxy resin E44 and 0.3mg / mL graphene aqueous solution were mixed at a volume ratio of 1:1, the temperature was controlled at 100°C and stirred for 10 minutes, and the layers were separated after standing still for 30 minutes. The upper layer of aqueous solution was poured out, and the lower layer of graphene - Continue to heat the epoxy resin at 90°C and stir for 10 hours, add epoxy resin curing agent H-1618 (Shijiazhuang Huili Chemical Co., Ltd., Shijiazhuang, Hebei, China), and cure at 100°C for 1 hour, and then cure at 150°C for 2 hours hours, a cured graphene-epoxy composite was obtained.
Embodiment 3
[0014] Trifunctional epoxy resin TDE-85 was mixed with 0.3 mg / mL graphene aqueous solution at a volume ratio of 1:1.5 (trifunctional epoxy resin TDE-85, Tianjin Jindong Chemical Plant, Tianjin, China), and the temperature was controlled at 90 Stir at ℃ for 20 minutes, stand still for 30 minutes to separate layers, pour out the upper layer of aqueous solution, continue to heat the lower layer of graphene-epoxy resin at 100°C and stir for 8 hours, add epoxy resin curing agent H-1618 (Shijiazhuang Huili Chemical Co., Ltd., Shijiazhuang, Hebei, China), and cured at 100°C for 1 hour, and then cured at 150°C for 2 hours to obtain a cured graphene-epoxy composite material.
PUM
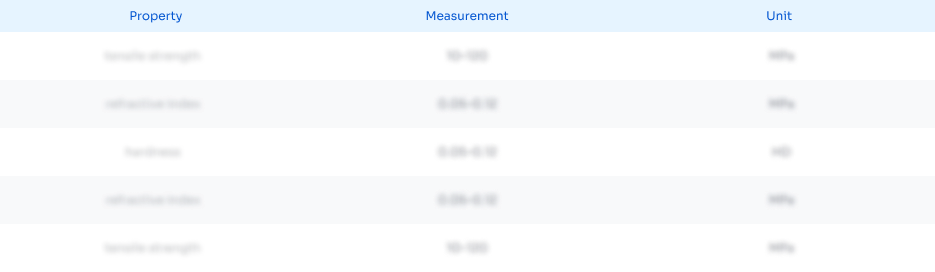
Abstract
Description
Claims
Application Information

- R&D
- Intellectual Property
- Life Sciences
- Materials
- Tech Scout
- Unparalleled Data Quality
- Higher Quality Content
- 60% Fewer Hallucinations
Browse by: Latest US Patents, China's latest patents, Technical Efficacy Thesaurus, Application Domain, Technology Topic, Popular Technical Reports.
© 2025 PatSnap. All rights reserved.Legal|Privacy policy|Modern Slavery Act Transparency Statement|Sitemap|About US| Contact US: help@patsnap.com