Steel plate multicomponent alloy co-cementation method
A technology of multi-element alloy co-infiltration and steel plate, which is applied in the direction of metal material coating process, coating, solid-state diffusion coating, etc., can solve the problems of easily changing the size of the steel plate and failing to achieve anti-corrosion performance, and achieve good results
- Summary
- Abstract
- Description
- Claims
- Application Information
AI Technical Summary
Problems solved by technology
Method used
Examples
Embodiment
[0020] Embodiment: a kind of multi-component alloy co-infiltration method for steel plate, comprising the following steps: 1. Prepare co-infiltration material first, add ammonium chloride and floating beads in powdery co-infiltration alloying elements, powdery alloying elements are weight ratio 1.6 % of Zn powder, 0.4% of Al powder, 0.13% of rare earth powder, ammonium chloride accounts for 0.1% by weight, and the rest is floating beads, the diameter of which is 3mm;
[0021] 2. Put the steel plate to be heat treated into the co-infiltration furnace and fix it. The steel plate and the steel plate are parallel and spaced apart from each other. The distance between the steel plates is 30mm. Put the co-infiltration material into the co-infiltration furnace and then seal the co-infiltration furnace. The weight ratio of steel plate to co-infiltration material is 3:1;
[0022] 3. Vacuum the co-infiltration furnace to -0.08 MPa, and start heating to 450°C at the same time, then keep ...
PUM
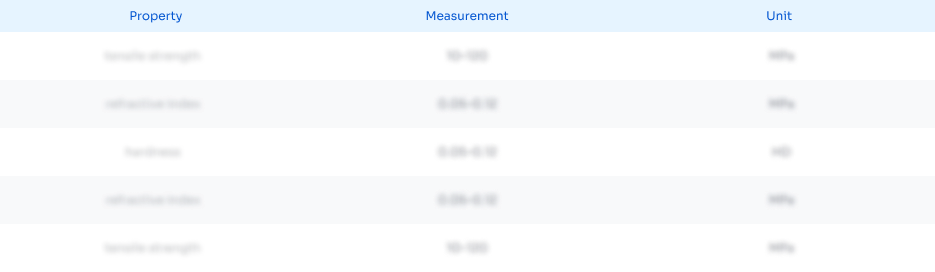
Abstract
Description
Claims
Application Information

- R&D
- Intellectual Property
- Life Sciences
- Materials
- Tech Scout
- Unparalleled Data Quality
- Higher Quality Content
- 60% Fewer Hallucinations
Browse by: Latest US Patents, China's latest patents, Technical Efficacy Thesaurus, Application Domain, Technology Topic, Popular Technical Reports.
© 2025 PatSnap. All rights reserved.Legal|Privacy policy|Modern Slavery Act Transparency Statement|Sitemap|About US| Contact US: help@patsnap.com