Method for preparing metal vanadium
A metal and crude vanadium technology, applied in the field of metallurgy, can solve the problems of high production cost, high electrolysis energy consumption, and high equipment requirements, and achieve the effects of low cost, simple process steps and broad application prospects.
- Summary
- Abstract
- Description
- Claims
- Application Information
AI Technical Summary
Problems solved by technology
Method used
Examples
preparation example Construction
[0020] a, the preparation of crude vanadium: take vanadium trioxide and vanadium pentoxide as raw materials, take Al powder as reducing agent, ignition reduction makes crude vanadium and slag; Wherein, the weight ratio of vanadium trioxide and vanadium pentoxide The ratio is 1:1~2, and the amount of Al powder is 0.6~0.9 times of the theoretical amount of V when the raw material is completely reduced;
[0021] b. Refining: Vacuum refining to obtain metal vanadium.
[0022] Wherein, in order to improve the purity of the prepared metal vanadium, the purity of the vanadium trioxide and vanadium pentoxide described in step a above is preferably ≥99.9%, and the purity of the Al powder is preferably ≥99.7%.
[0023] Wherein, because the vanadium content in the obtained slag of the present invention is higher, in order to make full use of the vanadium resource, avoid resource waste, the slag obtained in the above step a can be used as the lining of the reaction furnace, and can also b...
Embodiment 1
[0030] Embodiment 1 adopts the inventive method to prepare metal vanadium
[0031] Get 4000g of vanadium oxide mixture, wherein the weight ratio of vanadium trioxide and vanadium pentoxide is 1:1, and the aluminum powder addition ratio is 0.7 (that is, 0.7 times of theoretical aluminum consumption, the same below), to analyze The pure barium peroxide mixture is used as the ignition agent, and the aluminothermic reduction reaction is carried out in the aluminothermic reduction reaction furnace, and the reaction ends in 61 seconds. After the aluminothermic reaction is completed, 1650g of crude vanadium with a vanadium content (mass percentage, the same below) of 99.5% is generated, and the crude vanadium is put into a vacuum melting furnace, and melted for 4 hours at a vacuum degree of 0.255Pa and a melting temperature of 2000°C , remove nitrogen, oxygen, hydrogen, aluminum and other impurities to obtain 1600g of vacuum smelted product.
[0032] A part of the aluminothermic rea...
Embodiment 2
[0034] Embodiment 2 adopts the inventive method to prepare metal vanadium
[0035] Get 40kg of vanadium oxide mixture, wherein the weight ratio of vanadium trioxide and vanadium pentoxide is 1:2, the aluminum matching coefficient added by aluminum powder is 0.9, and the amount of limestone added is 2kg, with analytically pure barium peroxide as ignition agent , the aluminothermic reduction reaction is carried out in the aluminothermic reduction reaction furnace, and the reaction ends in 70 seconds. After the aluminothermic reaction is completed, 21kg of crude vanadium with a vanadium content of 99.4% is produced. Put the crude vanadium into a vacuum melting furnace and melt for 10 hours at a vacuum degree of 0.133Pa and a temperature of 2200°C to remove nitrogen, oxygen, hydrogen, aluminum, etc. Impurities were removed to obtain 20kg vacuum smelting product.
[0036] A part of the aluminothermic reaction slag is used as the lining of the aluminothermic reduction reaction furn...
PUM
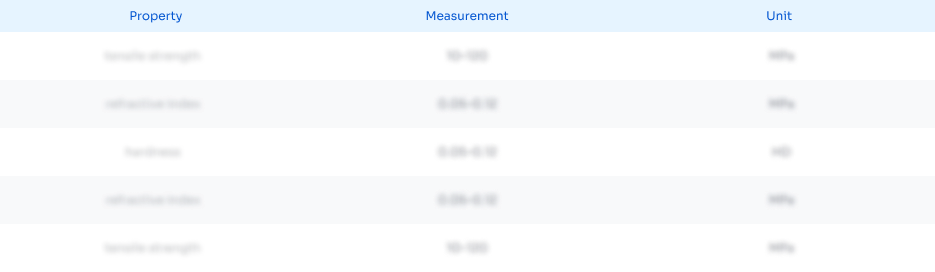
Abstract
Description
Claims
Application Information

- R&D
- Intellectual Property
- Life Sciences
- Materials
- Tech Scout
- Unparalleled Data Quality
- Higher Quality Content
- 60% Fewer Hallucinations
Browse by: Latest US Patents, China's latest patents, Technical Efficacy Thesaurus, Application Domain, Technology Topic, Popular Technical Reports.
© 2025 PatSnap. All rights reserved.Legal|Privacy policy|Modern Slavery Act Transparency Statement|Sitemap|About US| Contact US: help@patsnap.com