Method for catalytically oxidizing sulfocompound in petroleum product
A catalytic oxidation and compound technology, applied in the chemical industry, can solve the problems of slow reaction rate and small contact probability of reactants, and achieve the effects of high recovery rate, convenient separation and removal, and high conversion rate.
- Summary
- Abstract
- Description
- Claims
- Application Information
AI Technical Summary
Problems solved by technology
Method used
Examples
Embodiment 1
[0017] (1) The catalyst is added to the water phase (aqueous hydrogen peroxide solution with a mass concentration of 5%), stirred and dispersed at a rate of 100 rpm for 10 minutes, then added with gasoline with a sulfur content of 2500ppm to form a reaction system, at 80°C Stirring reaction at a rate of 1200 rpm under conditions for 10 minutes; the catalyst is talc, synthetic magnesium silicate, the talc of the load active component, the synthetic magnesium silicate of the load active component or the activated carbon of the load active component, so The above active components are one or more of molybdenum trioxide, tungsten trioxide, zinc oxide, ferric oxide, titanium dioxide, copper oxide, silicon dioxide, manganese dioxide, aluminum oxide, cerium oxide and lanthanum oxide , the mass ratio of the active component to talc, the mass ratio of the active component to synthetic magnesium silicate and the mass ratio of the active component to activated carbon are 0.15: 1, and the ...
Embodiment 2
[0022] (1) The catalyst is added into the water phase (aqueous hydrogen peroxide solution with a mass concentration of 30%), stirred and dispersed at a rate of 200 rpm for 20 minutes, and then added with a sulfur content of 500ppm diesel to form a reaction system, at 20°C Stirring reaction at a rate of 100 rev / min under conditions for 360 minutes; the catalyst is talc, synthetic magnesium silicate, the talc of the loaded active component, the synthetic magnesium silicate of the loaded active component or the activated carbon of the loaded active component, so The above active components are one or more of molybdenum trioxide, tungsten trioxide, zinc oxide, ferric oxide, titanium dioxide, copper oxide, silicon dioxide, manganese dioxide, aluminum oxide, cerium oxide and lanthanum oxide , the mass ratio of the active component to talc, the mass ratio of the active component to synthetic magnesium silicate and the mass ratio of the active component to activated carbon are all 0.3:...
Embodiment 3
[0027] (1) The catalyst is added to the water phase (aqueous hydrogen peroxide solution with a mass concentration of 50%), stirred and dispersed at a rate of 300 rpm for 1 minute, and then diesel oil with a sulfur content of 1500ppm is added to form a reaction system at 50°C Under the conditions with 650 rev / min speed stirring reaction 185 minutes; Described catalyst is the talc of talc, synthetic magnesium silicate, load active component, the synthetic magnesium silicate of load active component or the gac of load active component, so The above active components are one or more of molybdenum trioxide, tungsten trioxide, zinc oxide, ferric oxide, titanium dioxide, copper oxide, silicon dioxide, manganese dioxide, aluminum oxide, cerium oxide and lanthanum oxide , the mass ratio of the active component to talc, the mass ratio of the active component to synthetic magnesium silicate and the mass ratio of the active component to activated carbon are 0.01: 1, and the mass ratio of t...
PUM
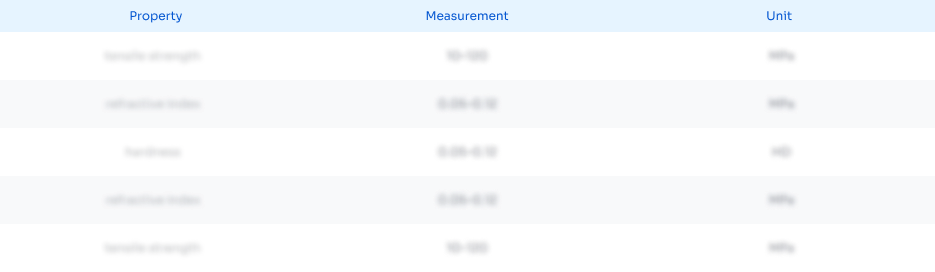
Abstract
Description
Claims
Application Information

- Generate Ideas
- Intellectual Property
- Life Sciences
- Materials
- Tech Scout
- Unparalleled Data Quality
- Higher Quality Content
- 60% Fewer Hallucinations
Browse by: Latest US Patents, China's latest patents, Technical Efficacy Thesaurus, Application Domain, Technology Topic, Popular Technical Reports.
© 2025 PatSnap. All rights reserved.Legal|Privacy policy|Modern Slavery Act Transparency Statement|Sitemap|About US| Contact US: help@patsnap.com