Production method of compound filter material
A production method and technology of composite filter material, applied in the field of filtration, can solve the problems of poor corrosion resistance, high cost, short service life, etc., and achieve the effects of long service life, high bending resistance and high wear resistance.
- Summary
- Abstract
- Description
- Claims
- Application Information
AI Technical Summary
Problems solved by technology
Method used
Examples
Embodiment Construction
[0007] Steps:
[0008] 1. Base fabric weaving:
[0009] The grammage is 600g / m by weaving with pure tass fiber yarn by loom 2 Metas fiber loom cloth, ready for use.
[0010] 2. Opening
[0011] Mix 1000kg of polyester, 150kg of acrylic fibers and 150kg of PPS fibers, place them in an opener, mix and open them evenly, and set aside.
[0012] 3. Combing
[0013] The opened acrylic fiber, PPS fiber and polyester fiber are carded and combed to form a mixed net layer.
[0014] 4. Laying net
[0015] Lay the mixed net layer on the two outer sides of the Metas fiber loom cloth respectively.
[0016] 5. Felting
[0017] Pre-stabbing is performed on the laid net first, and then the main stabbing is performed to make a semi-finished felt.
[0018] 6. The semi-finished felt is singed, calendered, and finally heat-set to form a composite filter material non-woven fabric.
[0019] 7. According to the needs, cut the composite filter material non-woven fabric to make block composite...
PUM
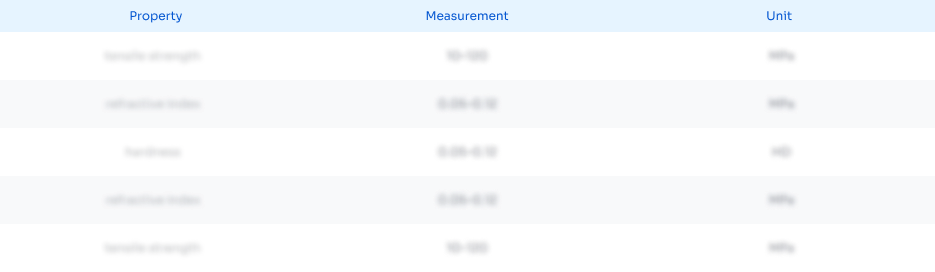
Abstract
Description
Claims
Application Information

- R&D Engineer
- R&D Manager
- IP Professional
- Industry Leading Data Capabilities
- Powerful AI technology
- Patent DNA Extraction
Browse by: Latest US Patents, China's latest patents, Technical Efficacy Thesaurus, Application Domain, Technology Topic, Popular Technical Reports.
© 2024 PatSnap. All rights reserved.Legal|Privacy policy|Modern Slavery Act Transparency Statement|Sitemap|About US| Contact US: help@patsnap.com