Surface laser cladding method of hydraulic support post and jack
A technology of hydraulic support column and laser cladding, which is applied in laser welding equipment, coating, metal material coating process, etc., can solve the problems of column performance failure, social harm, and electroplating layer is easy to fall off, etc., and achieves small distortion and deformation , heat-affected zone is small, the effect of improving hardness
- Summary
- Abstract
- Description
- Claims
- Application Information
AI Technical Summary
Problems solved by technology
Method used
Examples
Embodiment Construction
[0026] A surface laser cladding method for hydraulic support columns and jacks, characterized in that it includes the following process steps performed in sequence:
[0027] Process the surface of the column and jack to be clad → feed the mixed gas (argon, nitrogen, carbon dioxide) into the laser generator → power on the laser generator → generate the laser beam from the laser generator → reflect the laser beam by 3 reflectors → send the laser beam to the powder feeder Powder→focusing with focusing mirror→metal powder cladding on the surface of the column and jack→processing the surface of the column and jack→finished product;
[0028] In the step of processing the surface of the column to be clad and the jack, a numerically controlled lathe is used to turn and process the surface of the column and the jack;
[0029] The laser generator adopts the CO of model GS-TEL-6000 2 Laser generator, its working conditions are as follows:
[0030] Rated power: 6KW;
[0031] Voltage: D...
PUM
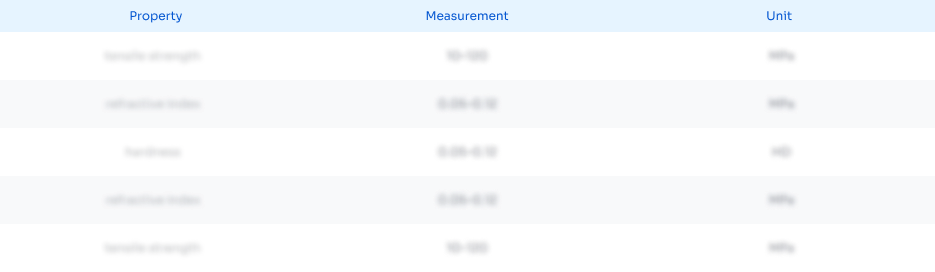
Abstract
Description
Claims
Application Information

- R&D
- Intellectual Property
- Life Sciences
- Materials
- Tech Scout
- Unparalleled Data Quality
- Higher Quality Content
- 60% Fewer Hallucinations
Browse by: Latest US Patents, China's latest patents, Technical Efficacy Thesaurus, Application Domain, Technology Topic, Popular Technical Reports.
© 2025 PatSnap. All rights reserved.Legal|Privacy policy|Modern Slavery Act Transparency Statement|Sitemap|About US| Contact US: help@patsnap.com