Carbon-based nano cast nylon composite material and in-situ polymerization preparation method thereof
A technology of carbon-based nano and composite materials, applied in chemical instruments and methods, conductive materials dispersed in non-conductive inorganic materials, and other chemical processes, to achieve the effects of simple preparation process, environmental friendliness, and easy control
- Summary
- Abstract
- Description
- Claims
- Application Information
AI Technical Summary
Problems solved by technology
Method used
Examples
Embodiment 1
[0034] Add 100 parts of caprolactam into a reaction kettle with an ultrasonic generator, melt the caprolactam at a temperature of 120°C, add 0.1 part of graphite oxide under the protection of nitrogen, and disperse the After 30 minutes, a graphite oxide caprolactam dispersion was obtained. At a temperature of 130°C and a vacuum of 0.098Mpa, dehydrate for 20 minutes. Then add 0.30 parts of sodium hydroxide as a catalyst, and continue vacuum dehydration for 30 minutes at a vacuum degree of 0.098Mpa. Open the valve to release the vacuum, add 0.5 parts of diphenylmethane diisocyanate (MDI) and 0.3 parts of dimethyl carbonate, stir quickly and evenly, then cast into a mold preheated to 165°C, keep it warm for 1 hour and then cool naturally. Obtain graphite oxide cast nylon nanocomposites.
Embodiment 2
[0036] Add 100 parts of caprolactam melt and 5 parts of graphene into a grinder, and grind at a temperature of 70° C. for 1.5 hours to obtain a graphene caprolactam dispersion. The above dispersion liquid was added into the reaction kettle, and vacuum dehydration was carried out at a temperature of 130° C. for 20 minutes with a vacuum degree of 0.05 MPa. Add 0.25 parts of sodium methoxide as a catalyst, and continue vacuum dehydration for 30 minutes at a vacuum degree of 0.05 MPa. Then add 0.7 parts by weight of toluene diisocyanate (TDI), stir quickly and evenly, then cast into a mold preheated to 160° C., keep warm for 1 hour and then cool naturally. That is, the graphene cast nylon nanocomposite material is obtained.
Embodiment 3
[0038] Add 100 parts of caprolactam into a reaction kettle with an ultrasonic generating device, melt the caprolactam at a temperature of 100°C, add 0.8 parts of graphite oxide under the protection of nitrogen, and disperse the After 30 minutes, a graphite oxide caprolactam dispersion was obtained. At a temperature of 130°C and a vacuum of 0.094Mpa, dehydrate for 20 minutes. Then add 0.40 part of sodium hydroxide and 0.20 part of sodium methoxide as a catalyst, and continue vacuum dehydration for 30 minutes at a vacuum degree of 0.094 Mpa. Open the valve to release the vacuum, add 0.5 parts of acetyl caprolactam, stir quickly and evenly, then cast it into a mold preheated to 165°C, keep it warm for 1 hour and then cool naturally. Obtain graphite oxide cast nylon nanocomposites.
PUM
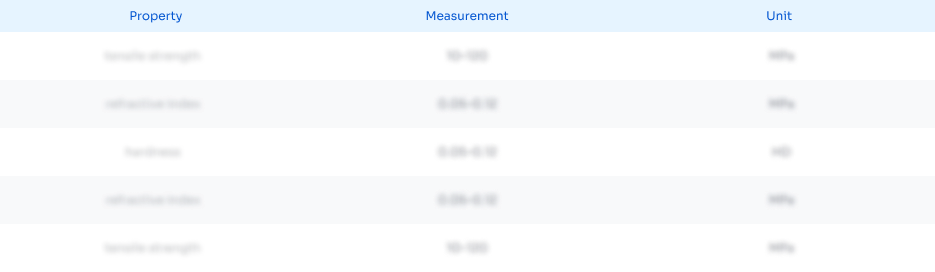
Abstract
Description
Claims
Application Information

- Generate Ideas
- Intellectual Property
- Life Sciences
- Materials
- Tech Scout
- Unparalleled Data Quality
- Higher Quality Content
- 60% Fewer Hallucinations
Browse by: Latest US Patents, China's latest patents, Technical Efficacy Thesaurus, Application Domain, Technology Topic, Popular Technical Reports.
© 2025 PatSnap. All rights reserved.Legal|Privacy policy|Modern Slavery Act Transparency Statement|Sitemap|About US| Contact US: help@patsnap.com