Method for epoxidating methyl oleate
A methyl oleate, epoxidation technology, applied in chemical instruments and methods, organic chemistry, chemical/physical processes, etc., can solve the problems of unstable organic peroxy acid, easy explosion, environmental pollution, etc., and achieve conversion rate. and high selectivity, mild reaction conditions, and short reaction times
- Summary
- Abstract
- Description
- Claims
- Application Information
AI Technical Summary
Problems solved by technology
Method used
Examples
Embodiment 1
[0024] Embodiment 1, 5.00g phosphotungstic heteropolyacid (H 3 o 40 PW 12 ) and 3.05g dioctadecyldimethylammonium chloride ((C 18 h 37 ) 2 N(CH 3 ) 2 Cl) were respectively dissolved in water (the molar ratio was 1:3), and then the aqueous solution of heteropolyacid was slowly added dropwise to the aqueous solution of dioctadecyldimethylammonium chloride at room temperature, and stirred at room temperature for 4 hours. The cloudy solution after the reaction was vacuum filtered, the filter cake was washed 3 times with water, then washed 3 times with ether, and dried in vacuum for 20 hours to obtain [(C 18 h 37 ) 2 N(CH 3 ) 2 ] 3 ·PW 12 o 40 (referred to as phosphotungstic acid-1821).
[0025] 20g methyl oleate (iodine value 80g / 100g, the same below) was added to the reactor (four-neck flask with agitator, reflux condenser, thermometer and dropping funnel, the same below), and 0.5g phosphorus Tungstic acid-1821 and 70g tetrahydrofuran, heated to 70°C and kept the t...
Embodiment 2
[0026] Embodiment 2, 5.00g phosphomolybdenum heteropolyacid (H 3 o 40 PMo 12 ) and 4.50g dioctadecyl dimethyl ammonium chloride ((C 18 h 37 ) 2 N(CH 3 ) 2 Cl) were respectively dissolved in a small amount of water (the molar ratio was 1:3.5), and then the heteropolyacid aqueous solution was slowly added dropwise to the aqueous solution of dioctadecyldimethylammonium chloride at room temperature, and stirred at room temperature for 5 hours . The cloudy solution after the reaction was vacuum filtered, the filter cake was washed 4 times with water, then 4 times with ether, and dried in vacuum for 25 hours to obtain [(C 18 h 37 ) 2 N(CH 3 ) 2 ] 3 ·PM 12 o 40 (referred to as phosphomolybdic acid-1821).
[0027] 20g methyl oleate is joined in the reactor, add 0.5g phosphomolybdic acid-1821 and 100g chloroform, heat to 70 ℃ and keep this temperature constant, slowly add dropwise 40mL hydrogen peroxide (30wt%), make hydrogen peroxide Finish dripping within 2 hours, and...
Embodiment 3
[0028] Embodiment 3, 5.00g phosphotungstic heteropolyacid (H 3 o 40 PW 12 ) and 3.25g dioctadecyl dimethyl ammonium chloride ((C 18 h 37 ) 2 N(CH 3 ) 2 Cl) were dissolved in water respectively (the molar ratio was 1:3.2), and then the aqueous heteropolyacid solution was slowly added dropwise to the aqueous solution of dioctadecyldimethylammonium chloride at room temperature, and stirred at room temperature for 4.5 hours. The cloudy solution after the reaction was vacuum filtered, the filter cake was washed 3 times with water, then 3 times with ether, and dried in vacuum for 23 hours to obtain [(C 18 h 37 ) 2 N(CH 3 ) 2 ] 3 ·PW 12 o 40 .
[0029]20g of methyl oleate was added to the reactor, 0.5g of phosphotungstic acid-1821 and 60g of 1,2-dichloroethane were added, heated to 70°C and the temperature was kept constant, and 40mL of hydrogen peroxide (30wt %), hydrogen peroxide was dripped within 2.5 hours, and then continued to insulate for 2 hours after the dropw...
PUM
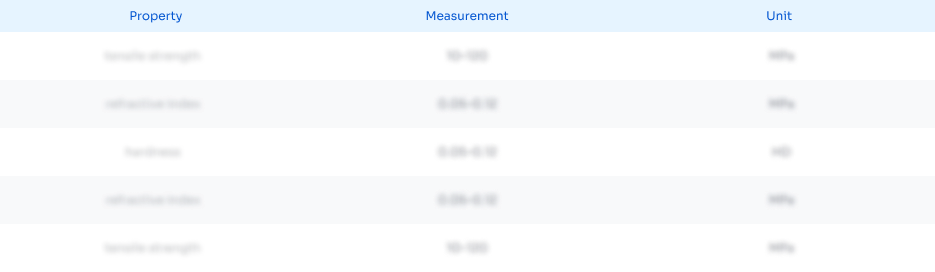
Abstract
Description
Claims
Application Information

- R&D
- Intellectual Property
- Life Sciences
- Materials
- Tech Scout
- Unparalleled Data Quality
- Higher Quality Content
- 60% Fewer Hallucinations
Browse by: Latest US Patents, China's latest patents, Technical Efficacy Thesaurus, Application Domain, Technology Topic, Popular Technical Reports.
© 2025 PatSnap. All rights reserved.Legal|Privacy policy|Modern Slavery Act Transparency Statement|Sitemap|About US| Contact US: help@patsnap.com