Micro-electrolytic environment-friendly filler, and production raw materials and preparation method thereof
A micro-electrolysis and environmental protection technology, applied in chemical instruments and methods, water/sewage treatment, water/sludge/sewage treatment, etc., can solve problems such as surface loss, easy passivation, and difficulty in popularization and use. The effects of solving system compaction and blockage, improving electrochemical activity, and facilitating popularization and utilization
- Summary
- Abstract
- Description
- Claims
- Application Information
AI Technical Summary
Problems solved by technology
Method used
Image
Examples
Embodiment 1
[0027] Such as figure 1 As shown in the flow chart, take a certain copper slag in Inner Mongolia, in which the iron oxide content is 64.3wt%, and the copper content is 1.8wt%. After drying, it is pulverized and ground, and passed through a 100-mesh sieve. The bituminous coal is ground and passed through a 100-mesh sieve. Sodium tetraborate is pulverized and ground and passed through a 100-mesh sieve for later use.
[0028] After the sieved copper slag, coal powder and sodium tetraborate are dried, they are fully mixed according to the mass ratio of 85:14:1 to obtain the carbon-matching copper slag powder. Spray a small amount of water to make the mixed powder have a certain viscosity, and then shape it to obtain carbon-copper slag balls. Put the carbon-copper slag balls into the reduction kiln, raise the temperature to 1150°C for 9 hours, keep the temperature for 9 hours, cool down for 6 hours, and then leave the kiln, after being crushed and sieved, the product-micro-electr...
Embodiment 2
[0030] Such as figure 1 As shown in the flow chart, take a certain copper slag in India, wherein the iron oxide content is 71.4wt%, and the copper content is 1.2wt%. After drying, it is pulverized and ground, and passed through a 100-mesh sieve. The coke powder is ground and passed through a 100-mesh sieve. Sodium tetraborate is pulverized and ground and passed through a 100-mesh sieve for later use.
[0031] After the sieved copper slag, coal powder and sodium tetraborate are dried, they are fully mixed according to the mass ratio of 60:35:5 to obtain the carbon-matched copper slag powder. Spray a small amount of water to make the mixed powder have a certain viscosity, and then shape it to obtain carbon-copper slag balls. Put the carbon-copper slag balls into the reduction furnace kiln, heat up for 6 hours to 1150 ° C for 9 hours, cool down for 6 hours, and then leave the kiln, and then sieve after crushing to obtain the product—micro-electrolytic environmental protection f...
Embodiment 3
[0033] Such as figure 1 As shown in the flow chart, take the tailings slag of a copper mine in Sichuan, wherein the iron oxide content is 58.7wt%, and the copper content is 7.4wt%. After drying, it is pulverized and ground, and passed through a 100-mesh sieve. The bituminous coal is ground and passed through a 100-mesh sieve. Sodium tetraborate is pulverized and ground and passed through a 100-mesh sieve for later use.
[0034]After drying the sieved copper slag, coal powder and sodium tetraborate, they are fully mixed according to the mass ratio of 80:19:1 to obtain carbon-matching copper slag powder. Spray a small amount of water to make the mixed powder have a certain viscosity, and then shape it to obtain carbon-copper slag balls. Put the carbon-copper slag balls into the reduction furnace kiln, heat up for 6 hours to 1150 ° C for 9 hours, cool down for 6 hours, and then leave the kiln, and then sieve after crushing to obtain the product—micro-electrolytic environmental ...
PUM
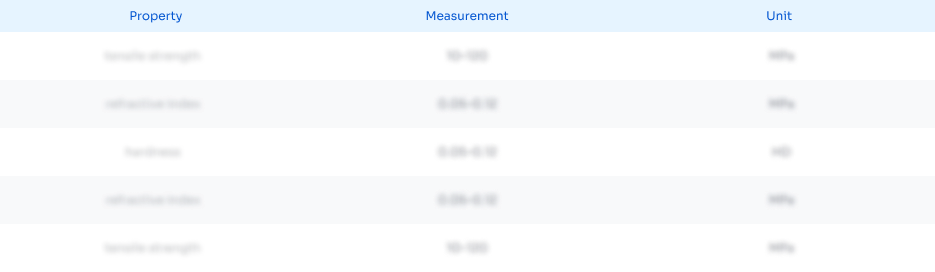
Abstract
Description
Claims
Application Information

- R&D Engineer
- R&D Manager
- IP Professional
- Industry Leading Data Capabilities
- Powerful AI technology
- Patent DNA Extraction
Browse by: Latest US Patents, China's latest patents, Technical Efficacy Thesaurus, Application Domain, Technology Topic, Popular Technical Reports.
© 2024 PatSnap. All rights reserved.Legal|Privacy policy|Modern Slavery Act Transparency Statement|Sitemap|About US| Contact US: help@patsnap.com