Glued laminated bamboo floor and manufacturing method thereof
A manufacturing method and glulam technology, applied in the direction of manufacturing tools, sustainable manufacturing/processing, wood processing equipment, etc., can solve the problems of low efficiency of billet assembly, poor gluing, dry glue, etc., to ensure strength and fatigue resistance, Effects of overcoming unstable bonding properties and reducing manufacturing costs
- Summary
- Abstract
- Description
- Claims
- Application Information
AI Technical Summary
Problems solved by technology
Method used
Image
Examples
Embodiment Construction
[0045] The present invention will be described in further detail below in conjunction with the accompanying drawings and specific embodiments.
[0046] Such as figure 2 Shown, the present embodiment product 12403mm, width is 305mm, and thickness is 28mm, and the composite unit bar of bamboo sheet adopts two layers of bamboo sheets to be stacked mutually, and bamboo sheet layer is glued laterally by 4 equal or unequal bamboo sheets Composition, except for the front and rear ends of the product, the length of other bamboo composite unit strips is 1000mm, and the bamboo composite unit strips are spliced in the longitudinal direction by means of finger joints. In this embodiment, each bamboo strip of adjacent bamboo composite unit strips The glued surfaces of the layers are not on the same line. The product of this embodiment can use isocyanate adhesives or melamine-modified urea-formaldehyde resin adhesives.
[0047] Such as image 3 As shown, the specific production steps of ...
PUM
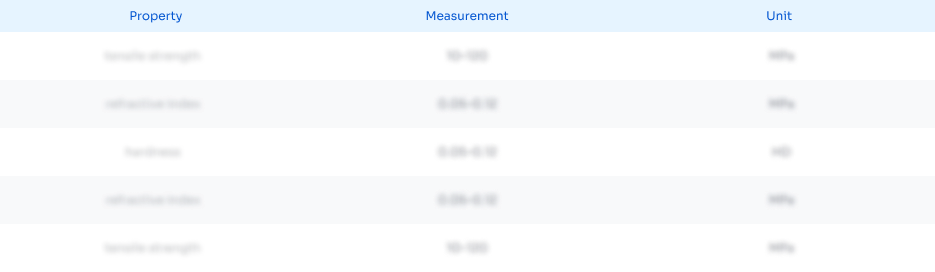
Abstract
Description
Claims
Application Information

- Generate Ideas
- Intellectual Property
- Life Sciences
- Materials
- Tech Scout
- Unparalleled Data Quality
- Higher Quality Content
- 60% Fewer Hallucinations
Browse by: Latest US Patents, China's latest patents, Technical Efficacy Thesaurus, Application Domain, Technology Topic, Popular Technical Reports.
© 2025 PatSnap. All rights reserved.Legal|Privacy policy|Modern Slavery Act Transparency Statement|Sitemap|About US| Contact US: help@patsnap.com