Preparation method of phenyl silicone resin
A technology of phenyl silicone resin and hydrocarbyl alkoxy silane is applied in the field of preparation of phenyl silicone resin, and can solve the problems of unguaranteed insulation stability and high temperature resistance of phenyl silicone resin.
- Summary
- Abstract
- Description
- Claims
- Application Information
AI Technical Summary
Problems solved by technology
Method used
Examples
Embodiment 1
[0028] Add 63g of ethyl orthosilicate, 146g of phenyltriethoxysilane, 34g of methylphenyldimethoxysilane, 5g of dimethyldiethoxysilane and 20g of tetramethyldisiloxane into 500ml In a four-neck flask, heat and stir for 10 minutes, add 1.7 g of concentrated hydrochloric acid, and then add 72 g of ultrapure water dropwise, and the dropping time is controlled at about 25 minutes. React at a constant temperature of 40°C for 3h, then raise the temperature to 90°C to remove low boilers. Then add 490g of ultrapure water, reflux at 80°C for 2 hours, cool, layer and separate, pour out the water layer, then add 490g of ultrapure water as residual resin, reflux at 80°C for 2h, cool, layer and separate, pour out the water layer, This was repeated three times, and the water layer was poured out, and the low boilers were removed under vacuum at 180°C, and after decolorization and filtration by activated carbon, a colorless, transparent and uniform phenyl hydrogen-containing silicone resin w...
Embodiment 2
[0030] 100g phenyltrimethoxysilane, 30g vinyltrimethoxysilane, 45g methyl orthosilicate, 24.3g diphenyldimethoxysilane, 10g dimethyldiethoxysilane, 18g 1, Add 3-divinyltetramethyldisiloxane and 10g hexamethyldisiloxane into a 500ml four-neck flask, heat and stir for 10min, add 3g of concentrated sulfuric acid, then dropwise add 45g of ultrapure water, dropwise The time is controlled at about 25 minutes. React at a constant temperature of 50°C for 3h, then raise the temperature to 90°C to remove low boilers. Transfer the resin to a 1L three-necked bottle, add 400g of ultrapure water, reflux at 90°C for 2 hours, cool, layer and separate the liquid, pour out the water layer, then add 400g of ultrapure water for the residual resin, reflux at 90°C for 2 hours, then cool, separate Separate the layers, pour out the water layer, and repeat this 4 times, pour out the water layer, remove the low boilers in vacuum at 180°C, decolorize and filter with activated carbon, and obtain a color...
Embodiment 3
[0032] Add 220g of phenyltrimethoxysilane, 12g of methyl orthosilicate, 15g of dimethyldiethoxysilane and 30g of end-blocking 1,3-divinyltetramethyldisiloxane into a 500ml four-port In the bottle, heat and stir for 10 minutes, add 2.8 g of concentrated sulfuric acid, and then add 37 g of ultrapure water dropwise, and the dropping time is controlled at about 25 minutes. React at a constant temperature of 70°C for 3h, then raise the temperature to 95°C to remove low boilers. Transfer the resin to a 1L three-necked bottle, add 470g of ultrapure water, reflux at 90°C for 2 hours, cool, layer and separate the liquid, pour out the water layer, then add 470g of ultrapure water for the residual resin, reflux at 95°C for 2 hours, then cool, separate Separate the layers, pour out the water layer, and repeat this 4 times, pour out the water layer, remove the low boilers in vacuum at 180°C, decolorize and filter with activated carbon, and obtain a colorless, transparent and uniform phenyl...
PUM
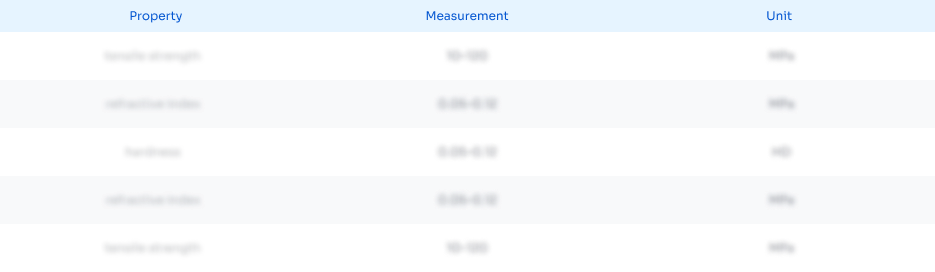
Abstract
Description
Claims
Application Information

- R&D Engineer
- R&D Manager
- IP Professional
- Industry Leading Data Capabilities
- Powerful AI technology
- Patent DNA Extraction
Browse by: Latest US Patents, China's latest patents, Technical Efficacy Thesaurus, Application Domain, Technology Topic, Popular Technical Reports.
© 2024 PatSnap. All rights reserved.Legal|Privacy policy|Modern Slavery Act Transparency Statement|Sitemap|About US| Contact US: help@patsnap.com