Down draft kiln
The technology of a reverse flame kiln and a furnace body is applied in the field of the reverse flame kiln, which can solve problems such as low thermal efficiency, and achieve the effects of increased flame volume, high calcination temperature, and uniform temperature distribution in the furnace.
- Summary
- Abstract
- Description
- Claims
- Application Information
AI Technical Summary
Problems solved by technology
Method used
Image
Examples
Embodiment 1
[0023] Furnace body 2 is composed of refractory brick layer 6, heat insulation layer 7, heat preservation layer 8 and shell 9. There are flue gas air inlet and outlet 5 on both sides of the bottom of furnace body 1, and there is heat storage body 10 inside flue gas air inlet and outlet 5. , above the flue gas air inlet and outlet 5, and located at the lower part of the furnace body 2, a fuel nozzle 3 is provided, between the flue gas air inlet and outlet 5 and the fuel nozzle 3, and there is a fire suction hole 11 in the furnace 22, and the fire suction hole There is a retaining wall 12 below the 11 to divide the flue gas air inlet and outlet 5 on both sides into two parts, and a temperature measuring hole 4 is arranged on the top of the furnace body 2 .
[0024] The kiln adopts advanced high-temperature air combustion technology to improve the traditional downdraft kiln, isolates the main flue of the traditional downdraft kiln along the center line, and installs regenerators a...
PUM
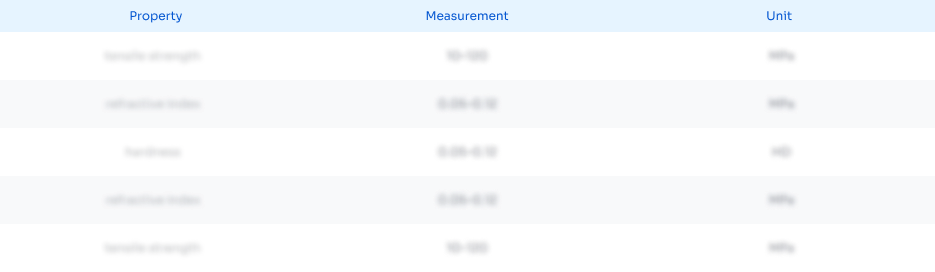
Abstract
Description
Claims
Application Information

- R&D
- Intellectual Property
- Life Sciences
- Materials
- Tech Scout
- Unparalleled Data Quality
- Higher Quality Content
- 60% Fewer Hallucinations
Browse by: Latest US Patents, China's latest patents, Technical Efficacy Thesaurus, Application Domain, Technology Topic, Popular Technical Reports.
© 2025 PatSnap. All rights reserved.Legal|Privacy policy|Modern Slavery Act Transparency Statement|Sitemap|About US| Contact US: help@patsnap.com