Manufacturing method of multi-functional modified acrylic fibers with high moisture absorption and flame resistance
A technology of modified acrylic fibers and manufacturing methods, applied in textiles and papermaking, fiber types, fiber treatment, etc., can solve the problems of secondary environmental pollution, easy generation of static electricity, poor hygroscopicity, etc., achieve good mechanical properties, simple production process, The effect of less investment in equipment
- Summary
- Abstract
- Description
- Claims
- Application Information
AI Technical Summary
Problems solved by technology
Method used
Examples
Embodiment 1
[0017] Take 7g of acrylic fiber, add it to 0.5% aqueous solution containing 15 times the amount of acrylic fiber by mass of copper sulfate, immerse and react at room temperature for 20 minutes, take it out, wash it and squeeze it dry. Then add the acrylic fibers containing copper ions into 6 times of the mixed solution composed of hydrazine hydrate, sodium hydroxide and surfactant and soak for 5 minutes. The mixed solution is composed of 5% hydrazine hydrate and 0.2% sodium hydroxide and a surfactant in a mass percentage concentration, and then the acrylic fiber is squeezed or dried into an aqueous acrylic fiber with a moisture content of 70%, and put into Dry-steam in a high-temperature and high-pressure steamer for 240 minutes at 130°C, take it out, wash it and dry it to obtain a highly hygroscopic flame-retardant acrylic fiber.
Embodiment 2
[0019] Take 8g of acrylic fiber, add it into an aqueous solution containing 1.0% copper sulfate with a mass percentage concentration of 12 times the amount of acrylic fiber, immerse and react at room temperature for 15 minutes, take it out, wash it and squeeze it dry. Then add the acrylic fibers containing copper ions to 7 times the mixed solution composed of hydrazine hydrate, sodium hydroxide, retarder and scouring agent and soak for 10 minutes. The mixed solution is composed of 10% hydrazine hydrate in mass percentage concentration, 0.5% sodium hydroxide in mass percentage concentration, 0.3% retarder and scouring agent in mass percentage concentration, and then the acrylic fiber is squeezed or dried to a moisture content of The 100% aqueous acrylic fiber is put into a high-temperature and high-pressure steamer and steamed for 200 minutes at 140° C., taken out, washed and dried to obtain a high-moisture-absorbing flame-retardant acrylic fiber.
Embodiment 3
[0021] Take 10g of acrylic fiber, add it to an aqueous solution containing 1.5% copper sulfate with a mass percentage concentration of 10 times the amount of acrylic fiber, react at 100° C. boiling water for 10 minutes, take it out, wash it, and spin it dry. Then the acrylic fibers containing copper ions are added to 8 times the mixed solution composed of hydrazine hydrate, sodium hydroxide, penetrating agent and leveling agent and soaked for 15 minutes. The mixed solution is 15% hydrazine hydrate with a mass percentage concentration of 1.0 % sodium hydroxide, 0.5% concentration of penetrating agent and leveling agent in mass percentage, then squeeze or dry the acrylic fiber into acrylic fiber with a water content of 150%, and put it into a high-temperature and high-pressure steaming pot Dry steam in a nitrogen atmosphere at 150°C for 150 minutes, take it out, wash it and dry it to obtain a highly hygroscopic flame-retardant acrylic fiber.
PUM
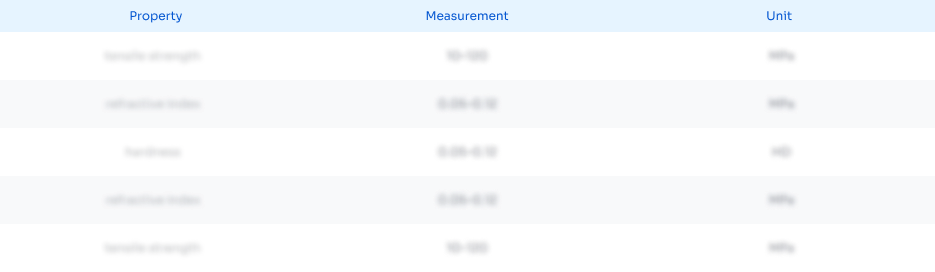
Abstract
Description
Claims
Application Information

- R&D
- Intellectual Property
- Life Sciences
- Materials
- Tech Scout
- Unparalleled Data Quality
- Higher Quality Content
- 60% Fewer Hallucinations
Browse by: Latest US Patents, China's latest patents, Technical Efficacy Thesaurus, Application Domain, Technology Topic, Popular Technical Reports.
© 2025 PatSnap. All rights reserved.Legal|Privacy policy|Modern Slavery Act Transparency Statement|Sitemap|About US| Contact US: help@patsnap.com