Method for preparing diphenyl hydrazine
A technology of diphenylhydrazine and nitrobenzene, which is applied in the preparation of hydrazine, organic chemistry, etc., can solve the problems of no industrial advantages, high price, and high cost, and achieve the effects of short reaction time, low cost, and high conversion rate
- Summary
- Abstract
- Description
- Claims
- Application Information
AI Technical Summary
Problems solved by technology
Method used
Examples
Embodiment 1
[0018] Preparation of Raney Nickel:
[0019] Add 20g of nickel aluminum alloy, 1g of copper chloride, and 2g of cobalt nitrate in batches to 80g of sodium hydroxide solution. After the addition, control the temperature at 80°C until almost no gas escapes. After cooling, wash with sodium hydroxide solution, then wash with distilled water to near neutrality, wash with methanol for 3 times, and then soak in appropriate amount of methanol to prevent Raney nickel from contacting with air.
[0020] Preparation of diphenylhydrazine:
[0021] Add 50g of nitrobenzene, 150g of anhydrous methanol, 60g of sodium hydroxide and 5g of Raney nickel into the stainless steel reaction kettle, feed 0.05MPa of ammonia gas, keep the pressure of hydrogen at 0.8MPa, stir and react at room temperature for 5 hours, then unload Press, pour out the reaction solution, stir and soak the catalyst at the bottom of the kettle once with 20g of methanol (the catalyst can be used mechanically), combine the Rane...
Embodiment 2
[0023] Preparation of Raney Nickel:
[0024] Add 20g of nickel aluminum alloy, 1g of copper chloride, and 2g of cobalt nitrate in batches to 80g of sodium hydroxide solution. After the addition, control the temperature at 80°C until almost no gas escapes. After cooling, wash with sodium hydroxide solution, then wash with distilled water to near neutrality, wash with methanol for 3 times, and then soak in appropriate amount of methanol to prevent Raney nickel from contacting with air.
[0025] Preparation of diphenylhydrazine:
[0026] Add 50g of nitrobenzene, 200g of anhydrous methanol, 80g of sodium hydroxide and 7g of Raney nickel into the stainless steel reaction kettle, feed 0.10MPa of ammonia gas, keep the hydrogen pressure stable at 0.6MPa, stir and react at room temperature for 12 hours, then unload Press, pour out the reaction solution, stir and soak the catalyst at the bottom of the kettle once with 30g of methanol (the catalyst can be used mechanically), combine the...
PUM
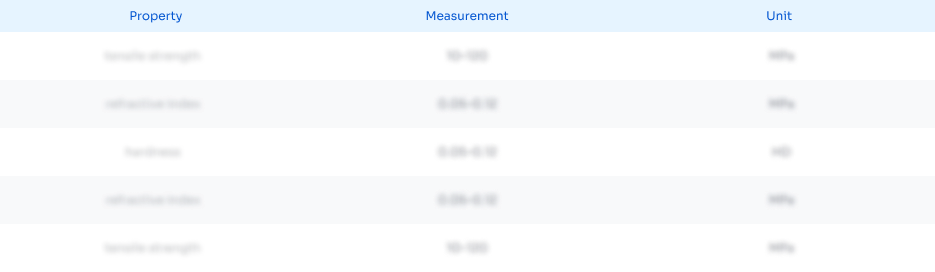
Abstract
Description
Claims
Application Information

- Generate Ideas
- Intellectual Property
- Life Sciences
- Materials
- Tech Scout
- Unparalleled Data Quality
- Higher Quality Content
- 60% Fewer Hallucinations
Browse by: Latest US Patents, China's latest patents, Technical Efficacy Thesaurus, Application Domain, Technology Topic, Popular Technical Reports.
© 2025 PatSnap. All rights reserved.Legal|Privacy policy|Modern Slavery Act Transparency Statement|Sitemap|About US| Contact US: help@patsnap.com