Thin porcelain brick and production method thereof
A ceramic tile, thin technology, applied in building construction, covering/lining, construction, etc., can solve the problems that affect the comprehensive performance of products, increase process and cost, increase special equipment, etc., to achieve smooth powder particles, heat transfer, etc. The effect of fast and prolonged holding time
- Summary
- Abstract
- Description
- Claims
- Application Information
AI Technical Summary
Problems solved by technology
Method used
Examples
Embodiment 1
[0025] The green body raw materials are composed of the following components by weight: ball clay 4.9%, black mud 5.9%, Yichun kaolin 7.9%, Beihai kaolin 9.9%, Dehua pyrophyllite 13.0%, Paishan pyrophyllite 9.9%, potassium albite feldspar powder 12.0% , weathered potassium feldspar 12.0%, super porcelain stone 8.8%, potassium albite feldspar 8.8%, Zhuji porcelain sand 5.9%, lignin R-OH 0.3%, lignin derivatives 0.7%. Thin porcelain tiles are fired through the method of Example 6.
Embodiment 2
[0027] The green body raw materials are composed of the following components by weight: ball clay 5.0%, black mud 5.9%, Yichun kaolin 6.9%, Beihai kaolin 8.9%, Dehua pyrophyllite 7.9%, Paishan pyrophyllite 7.8%, potassium albite powder 15.0% , weathered potassium feldspar 15.0%, super porcelain stone 9.8%, potassium albite feldspar 11.0%, Zhuji porcelain sand 5.8%, lignin R-OH 0.5%, lignin derivatives 0.5%. Thin porcelain tiles are fired through the method of Example 6.
Embodiment 3
[0029] The green body raw materials are composed of the following components by weight: ball clay 5.0%, black mud 5.0%, Yichun kaolin 6.0%, Beihai kaolin 6.0%, Dehua pyrophyllite 7.8%, Paishan pyrophyllite 6.0%, potassium albite powder 14.8% , weathered potassium feldspar 14.8%, super porcelain stone 12.8%, potassium albite feldspar 15.0%, Zhuji porcelain sand 6.0%, lignin derivatives 0.8%. Thin porcelain tiles are fired through the method of Example 6.
PUM
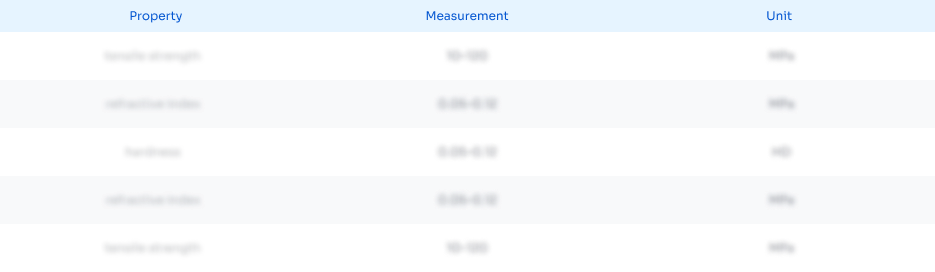
Abstract
Description
Claims
Application Information

- R&D
- Intellectual Property
- Life Sciences
- Materials
- Tech Scout
- Unparalleled Data Quality
- Higher Quality Content
- 60% Fewer Hallucinations
Browse by: Latest US Patents, China's latest patents, Technical Efficacy Thesaurus, Application Domain, Technology Topic, Popular Technical Reports.
© 2025 PatSnap. All rights reserved.Legal|Privacy policy|Modern Slavery Act Transparency Statement|Sitemap|About US| Contact US: help@patsnap.com