Magnesium alloy surface conversion coating treating fluid and treating process thereof
A technology for treating liquid and conversion film, which is applied in the coating process of metal materials, etc., can solve problems such as non-compliance with environmental protection and environmental pollution, and achieve the effect of easy control of the process, stable process and less additives
- Summary
- Abstract
- Description
- Claims
- Application Information
AI Technical Summary
Problems solved by technology
Method used
Image
Examples
Embodiment 1
[0013] The AZ60 magnesium alloy extrusion samples were processed.
[0014] Prepare magnesium alloy treatment solution by following formula:
[0015] Calcium Oxide 1.2 g / liter of aqueous solution
[0016] Phosphoric acid 8ml / liter aqueous solution
[0017] Calcium nitrate 10 grams per liter of aqueous solution
[0018] Sodium m-nitrobenzene sulfonate 1.5 g / liter aqueous solution
[0019] Calcium nitrite 0.8 g / liter aqueous solution
[0020] Degrease the surface of the AZ60 magnesium alloy sample and remove the oxide film, wash it with water, then put it into and immerse it in the above-mentioned prepared treatment solution adjusted to a pH value of 3.2 with phosphoric acid or sodium hydroxide, and let it stand at 40°C for 40 minutes , and then rinse with water, then dry. At this time, after the electrochemical polarization curve test, the self-corrosion voltage increased from the original -1.5mV to -0.89mV, and the self-corrosion current increased from the original 3.2×10 ...
Embodiment 2
[0022] The AZ60 magnesium alloy extrusion sample was processed.
[0023] Prepare magnesium alloy treatment solution by following formula:
[0024] Calcium Oxide 0.8 g / liter aqueous solution
[0025] Phosphoric acid 6ml / liter aqueous solution
[0026] Calcium nitrate 4 grams per liter of aqueous solution
[0027] Sodium m-nitrobenzene sulfonate 0.5 g / liter aqueous solution
[0028] Degrease the surface of the AZ60 magnesium alloy sample and remove the oxide film, wash it with water, then put it into and immerse it in the above-mentioned prepared treatment solution adjusted to PH value of 2.9 with phosphoric acid or sodium hydroxide, and let it stand at 50°C for 30 minutes , then washed with water and dried. After the electrochemical polarization curve test, the self-corrosion voltage increased from the original -1.49mV to -0.67mV, and the self-corrosion current increased from the original 3.0×10 -3 A / cm 2 up to 2.90×10 -5 A / cm 2 .
[0029] It can be seen from the implem...
Embodiment 3
[0031] The AZ91D magnesium alloy extrusion sample was processed.
[0032] Prepare magnesium alloy treatment solution by following formula:
[0033] Calcium Oxide 0.8 g / liter aqueous solution
[0034] Phosphoric acid 8ml / liter aqueous solution
[0035] Calcium nitrate 8 grams per liter of aqueous solution
[0036] Sodium m-nitrobenzene sulfonate 1.5 g / liter aqueous solution
[0037] Calcium nitrite 0.5 g / liter aqueous solution
[0038] Degrease the surface of the AZ91D magnesium alloy and remove the oxide film, wash it with water, then immerse it in the conversion solution prepared above to adjust the pH value to 3.1 with phosphoric acid or sodium hydroxide, let it stand at 40°C for 30 minutes, and then use water After washing, tumble dry. After the electrochemical polarization curve test, the self-corrosion voltage rose from -1.47mV to -1.22mV, and the self-corrosion current increased from -0.25A / cm 2 up to 6.3×10 -4 A / cm 2 .
PUM
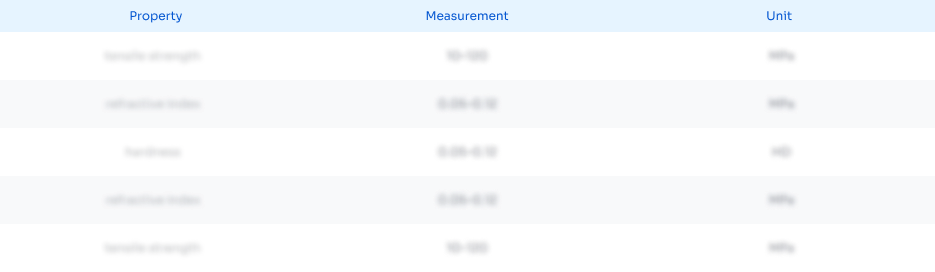
Abstract
Description
Claims
Application Information

- R&D
- Intellectual Property
- Life Sciences
- Materials
- Tech Scout
- Unparalleled Data Quality
- Higher Quality Content
- 60% Fewer Hallucinations
Browse by: Latest US Patents, China's latest patents, Technical Efficacy Thesaurus, Application Domain, Technology Topic, Popular Technical Reports.
© 2025 PatSnap. All rights reserved.Legal|Privacy policy|Modern Slavery Act Transparency Statement|Sitemap|About US| Contact US: help@patsnap.com