Process for 1,3-butadiene separation from crude C4 stream with acetylene converter
一种丁二烯、物流的技术,应用在蒸馏纯化/分离、有机化学、烃油处理产品等方向,能够解决氢气溶解达不到比值等问题,达到回收率增大、降低物流损失、装置数量减少的效果
- Summary
- Abstract
- Description
- Claims
- Application Information
AI Technical Summary
Problems solved by technology
Method used
Image
Examples
Embodiment 1
[0067] Acetylene conversion
[0068] A small scale test was carried out with a crude C4 stream having the composition shown in Table 3 below. The diameter of the pilot reactor was 6 cm and the length was 120 cm; the amount of catalyst in each reactor was 900 cc and the flow rate of the material was 9 L / hr; the three reactors were connected in sequence without recirculation. Catalyst G-68SK purchased from Sud-Chemie Catalysts Japan, Inc. was used as the catalyst for the hydrogenation of acetylene. Furthermore, internal coolers are provided between the reactors so that the temperature of the streams to be introduced into the reactors remains constant. As shown in Table 1, crude C4 stream 1 contains about 44-50% by weight of 1,3-butadiene and 1.2-2% by weight of acetylene. The feed temperature to each reactor was about 40-50°C, and the feed pressure was 30-31 bar. LHSV for each reactor is 10hr -1 , and respectively introduce hydrogen into the three reactors at a rate of 34.6N...
Embodiment 2
[0080] High-purity 1,3-butadiene is separated and obtained in the same manner as in Example 1, the difference is that, as figure 2 As shown, a portion 21-1 of the effluent 1-3 of the third reactor R3 (the same amount as the crude C4 stream 1) is introduced into the first reactor together with the crude C4 stream 1 . The advantage is that the concentration of vinyl acetylene in the stream introduced into the first reactor R1 can be reduced to half of the concentration of vinyl acetylene when the recycling process is not used, thereby improving the activity stability and selectivity of the catalyst. The LHSV of each reactor is 20hr -1 .
[0081] A stream containing 42 wt. ppm vinyl acetylene was obtained from the acetylene conversion process, and through the subsequent extraction process, the recovery rate of 99.6 wt. % 1,3-butadiene (which contained 11 wt. ppm vinyl acetylene) reached 98.9 % by weight or higher (recovery of 97.9% by weight considering losses in the reactor). ...
Embodiment 3
[0087] High-purity 1,3-butadiene is separated and obtained in the same manner as in Example 1, the difference is that, as image 3 As shown, a portion 21-2 of the overhead stream of the extractive distillation column D2 is recycled to the first reactor in a predetermined amount together with the crude C4 stream. The advantage of recycling the overhead effluent 21-2 of the extractive distillation column D2 is that the initial concentration of vinyl acetylene and the concentration of 1,3-butadiene introduced into the first reactor R1 can be reduced to predetermined level, thereby improving the activity stability and selectivity of the catalyst. When 67% of the overhead stream 5 of extractive distillation column D2 is used as recycle stream 21-2, the crude C4 stream 1 accounts for 46.7% by weight of butadiene and 1.3% by weight of the total amount of said stream 1 The concentration of vinyl acetylene was reduced to 35.1% by weight and 0.99% by weight of the total amount of strea...
PUM
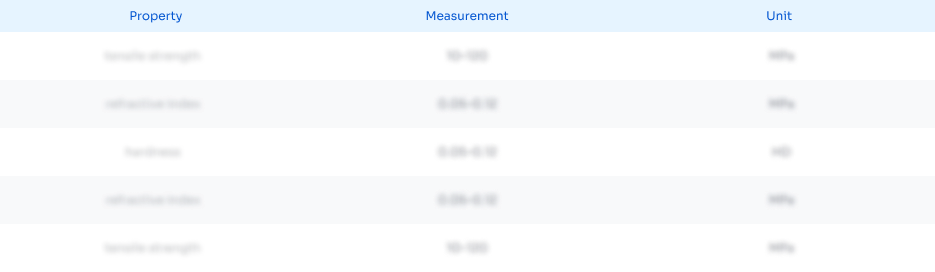
Abstract
Description
Claims
Application Information

- R&D
- Intellectual Property
- Life Sciences
- Materials
- Tech Scout
- Unparalleled Data Quality
- Higher Quality Content
- 60% Fewer Hallucinations
Browse by: Latest US Patents, China's latest patents, Technical Efficacy Thesaurus, Application Domain, Technology Topic, Popular Technical Reports.
© 2025 PatSnap. All rights reserved.Legal|Privacy policy|Modern Slavery Act Transparency Statement|Sitemap|About US| Contact US: help@patsnap.com