Method for preparing crosslinkable polyethylene insulated cable material
A cross-linked polyethylene, insulated cable technology, applied in the direction of organic insulators, plastic/resin/wax insulators, etc., can solve the problem of increasing the chance and time of LDPE heating and mechanical shearing, difficult to use high-grade insulating cable materials, increasing polymer Thermal oxidation and other problems to achieve the effect of meeting performance requirements, high processing stability and uniform distribution
- Summary
- Abstract
- Description
- Claims
- Application Information
AI Technical Summary
Problems solved by technology
Method used
Examples
Embodiment 1
[0012] 1) Dissolve β(3,5-di-tert-butyl-4-hydroxyphenyl) octadecyl propionate and dilauryl thiodipropionate in dissolved diisopropyl peroxide at a mass ratio of 1:1 In benzene, the total mass of beta (3,5-di-tert-butyl-4-hydroxyphenyl) octadecyl propionate and dilauryl thiodipropionate is 8% of dicumyl peroxide, mixed Evenly, to obtain liquid composite additives, use 800 mesh filter to remove impurities in the liquid composite additives;
[0013] 2) Mix the liquid compounding aid and the low-density polyethylene pellets at a mass ratio of 2:100 at 80°C for 1.5 hours, and through the liquid-solid diffusion between the liquid compounding aid and the low-density polyethylene pellets, the liquid Compounding additives are evenly absorbed by low-density polyethylene pellets. Then diffuse at a constant temperature of 80° C. for 15 hours to obtain a cross-linkable polyethylene insulating cable material.
Embodiment 2
[0015] 1) Mix 2,2'-thiobis[3-(3,5-di-tert-butyl-4-hydroxyphenyl) ethyl propionate] and distearyl thiodipropionate in a mass ratio of 1 : 2 dissolved in dissolved dicumyl peroxide, 2,2'-thiobis[3-(3,5-di-tert-butyl-4-hydroxyphenyl) ethyl propionate] and thiobis The total mass of Distearyl Propionate is 25% of dicumyl peroxide, mix uniformly to obtain the liquid composite auxiliary agent, and remove impurities in the liquid composite auxiliary agent with 2500 mesh filter screens;
[0016] 2) Mix the liquid compounding aid and the low-density polyethylene pellets at a mass ratio of 3:100 at 60°C for 2 hours, and through the liquid-solid diffusion between the liquid compounding aid and the low-density polyethylene pellets, the liquid compounding The additives are absorbed evenly by the LDPE pellets. Then diffuse at a constant temperature of 60° C. for 35 hours to obtain a cross-linkable polyethylene insulating cable material.
Embodiment 3
[0018] 1) Dissolve tetrakis[methyl-β-(3,5-di-tert-butyl-4-hydroxyphenyl)propionate]pentaerythritol ester and dilauryl thiodipropionate in the dissolving solution at a mass ratio of 1:1.5 The total mass of tetrakis[methyl-β-(3,5-di-tert-butyl-4-hydroxyphenyl) propionate] pentaerythritol ester and dilauryl thiodipropionate in dicumyl peroxide 15% of dicumyl peroxide, mixed uniformly to obtain a liquid composite additive, and a 2500-mesh filter screen was used to remove impurities in the liquid composite additive;
[0019] 2) Mix the liquid compounding aid and low-density polyethylene pellets at a mass ratio of 1.5:100 at 60°C for 2 hours, and through the liquid-solid diffusion between the liquid compounding aid and low-density polyethylene pellets, the liquid compounding The additives are absorbed evenly by the LDPE pellets. Then diffuse at a constant temperature of 70°C for 25 hours to obtain a cross-linkable polyethylene insulating cable material.
PUM
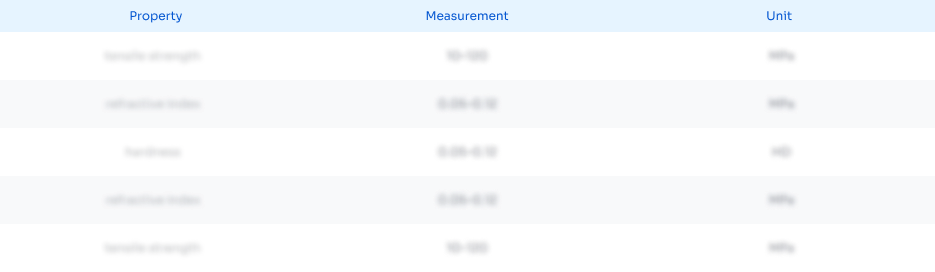
Abstract
Description
Claims
Application Information

- R&D
- Intellectual Property
- Life Sciences
- Materials
- Tech Scout
- Unparalleled Data Quality
- Higher Quality Content
- 60% Fewer Hallucinations
Browse by: Latest US Patents, China's latest patents, Technical Efficacy Thesaurus, Application Domain, Technology Topic, Popular Technical Reports.
© 2025 PatSnap. All rights reserved.Legal|Privacy policy|Modern Slavery Act Transparency Statement|Sitemap|About US| Contact US: help@patsnap.com