Low-cost method for disposing red soil nickel ore
A kind of laterite nickel ore, low-cost technology, applied in the field of nickel ore smelting, can solve the problems of nickel leaching rate of only 90%, long reaction time, difficult leaching, etc. The effect of liquid discharge
- Summary
- Abstract
- Description
- Claims
- Application Information
AI Technical Summary
Problems solved by technology
Method used
Image
Examples
Embodiment 1
[0027] (1) the ore sample 1 # Put into a stirring tank under normal pressure, add sulfuric acid for leaching for 2 hours according to the acid ore mass ratio of 0.53, and obtain two parts of filtrate a and filter residue b after the obtained pulp is filtered; filtrate a is sent to the recovery process of nickel, cobalt, magnesium and aluminum;
[0028] (2) Carry out magnetic separation to filter residue b, be divided into magnetic part c and non-magnetic part d;
[0029] (3) The magnetic part c is sent into the autoclave, and sulfuric acid is added according to the acid ore mass ratio of 0.55, reacted at 240°C for 1.5h, and the obtained pulp is filtered to obtain the filter residue e and the filtrate f;
[0030] (4) The filter residue e is used for iron recovery, and the filtrate f is returned to step (1).
[0031] After this every time new ore material adds, the sulfuric acid that newly adds is 0.1 to add by acid ore mass ratio; Collect the product that above-mentioned react...
Embodiment 2
[0033] (1) the ore sample 2 # Put into a stirring tank under normal pressure, add sulfuric acid for leaching for 2 hours according to the acid ore mass ratio of 0.58, and obtain two parts of filtrate a and filter residue b after filtering the obtained pulp;
[0034] (2) filtrate a is sent to the recovery process of nickel-cobalt-magnesium-aluminum;
[0035] (3) Carry out magnetic separation to filter residue b, be divided into magnetic part c and non-magnetic part d;
[0036](4) Put the magnetic part c into the autoclave, add sulfuric acid according to the acid ore mass ratio of 0.55, and add a small amount of oxygen to react at 260°C for 1.5h, and filter the obtained pulp to obtain filter residue e and filtrate f;
[0037] (5) The filter residue e is used for iron recovery, and the filtrate f is returned to step (1).
[0038] Thereafter, when new ore materials are added each time, the newly added sulfuric acid is added at a mass ratio of 0.15 to acid ore.
[0039] Collect ...
Embodiment 3
[0041] (1) the ore sample 1 # and sample 3 # Put into the atmospheric pressure stirring tank according to the ratio of 3:1 (mass ratio), add sulfuric acid to leach for 2 hours according to the acid ore mass ratio of 0.4, and obtain the filtrate a and the filter residue b after the obtained pulp is filtered;
[0042] (2) filtrate a is sent to the recovery process of nickel-cobalt-magnesium-aluminum;
[0043] (3) Carry out magnetic separation to filter residue b, be divided into magnetic part c and non-magnetic part d;
[0044] (4) The magnetic part c is sent into an autoclave, and sulfuric acid is added according to the acid ore mass ratio of 0.55, reacted at 220°C for 1.5h, and the obtained pulp is filtered to obtain filter residue e and filtrate f;
[0045] (5) The filter residue e is used for iron recovery, and the filtrate f is returned to step (1).
[0046] Thereafter, sulfuric acid is not added every time a new ore is added.
[0047] Collect the product of above-menti...
PUM
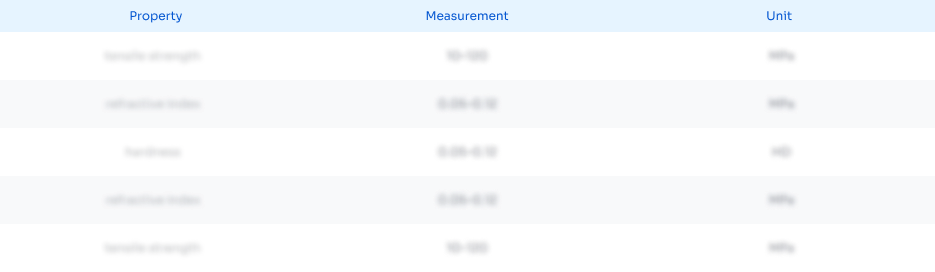
Abstract
Description
Claims
Application Information

- R&D
- Intellectual Property
- Life Sciences
- Materials
- Tech Scout
- Unparalleled Data Quality
- Higher Quality Content
- 60% Fewer Hallucinations
Browse by: Latest US Patents, China's latest patents, Technical Efficacy Thesaurus, Application Domain, Technology Topic, Popular Technical Reports.
© 2025 PatSnap. All rights reserved.Legal|Privacy policy|Modern Slavery Act Transparency Statement|Sitemap|About US| Contact US: help@patsnap.com