Heat-resistant halogen-free flame-retardant polylactic acid multi-element composite material and preparation method thereof
A composite material and polylactic acid technology, which is applied in the field of heat-resistant halogen-free flame-retardant polylactic acid multi-composite materials and their preparation, can solve the problems of substandard impact resistance, lack of compatibility, extrusion and puffing, and achieve improved toughness, Improved heat resistance and cost-effective effects
- Summary
- Abstract
- Description
- Claims
- Application Information
AI Technical Summary
Problems solved by technology
Method used
Examples
preparation example Construction
[0049] Preparation of modified polylactic acid resin:
[0050] Dry the polylactic acid resin in a vacuum oven at 45°C for 3-4 hours, weigh the dried PLA resin, maleic anhydride and initiator dicumyl peroxide DCP, and the weight ratio of the three is 100:5:0.5 , and then mixed evenly, extruded and granulated by co-rotating twin-screw extruder. The processing technology of the co-rotating twin-screw extruder is as follows: the temperature of the first zone is 150-180°C, the temperature of the second zone is 150-180°C, the temperature of the third zone is 150-180°C, the temperature of the fourth zone is 150-180°C, the temperature of the head is 170, the host The rotational speed is 400 rpm.
Embodiment 1
[0052] A heat-resistant halogen-free flame-retardant polylactic acid multi-component composite material is made of the following raw materials in parts by weight:
[0053] 37.6 parts of modified polylactic acid resin; 45.0 parts of bisphenol A polycarbonate resin; 10.0 parts of polybutylene succinate; 0.5 parts of dicumyl peroxide; 0.1 parts of white oil; 4.9 parts of PX-2000; 0.1 part of ketone powder; 1 part of ethylene bis stearic acid amide; 0.2 part of tetrakis [3-(3,5-di-tert-butyl-4-hydroxyphenyl)propionic acid] pentaerythritol ester, tris(2,4 phosphite - 0.1 part of di-tert-butylphenyl) ester; 0.7 part of hydrolysis inhibitor (ADR-4370), 0.3 part of ultraviolet absorber (UV-5411).
[0054] The preparation of heat-resistant halogen-free flame-retardant polylactic acid multi-component composite material includes the following steps
[0055] a: first dry the modified polylactic acid resin in a vacuum oven at 45°C for 3 hours;
[0056] b: Mix the dried modified polylactic ...
Embodiment 2
[0060] Example 2, a heat-resistant halogen-free flame-retardant polylactic acid multi-component composite material, made of the following raw materials in parts by weight: 32.7 parts of modified polylactic acid resin; 28.0 parts of bisphenol A polycarbonate resin; 25.0 parts of butylene glycol esters; 0.2 parts of dicumyl peroxide; 0.2 parts of white oil; 10 parts of PX-200; 1 part of silicone powder; , 0.1 part of 5-di-tert-butyl-4-hydroxyphenyl) propionate] pentaerythritol ester, 0.1 part of tris(2,4-di-tert-butylphenyl phosphite); 0.6 part of hydrolysis inhibitor (ADR-4370), 0.2 part of ultraviolet absorber (UV-5411).
[0061] The preparation of the heat-resistant halogen-free flame-retardant polylactic acid composite material comprises the following steps:
[0062] a: first dry the modified polylactic acid resin in a vacuum oven at 45°C for 4 hours;
[0063] b: Mix the dried modified polylactic acid resin and white oil in a high-speed mixer;
[0064] c: Mix the crosslin...
PUM
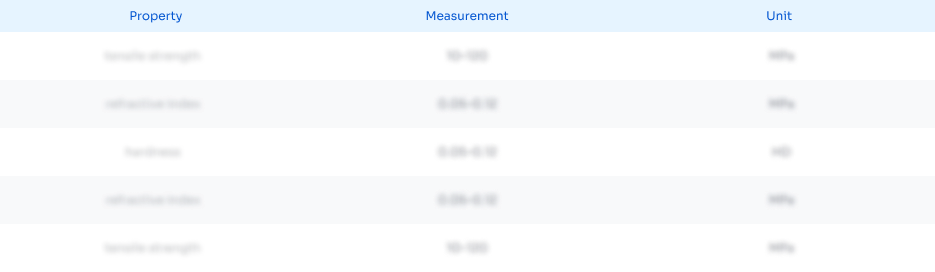
Abstract
Description
Claims
Application Information

- R&D
- Intellectual Property
- Life Sciences
- Materials
- Tech Scout
- Unparalleled Data Quality
- Higher Quality Content
- 60% Fewer Hallucinations
Browse by: Latest US Patents, China's latest patents, Technical Efficacy Thesaurus, Application Domain, Technology Topic, Popular Technical Reports.
© 2025 PatSnap. All rights reserved.Legal|Privacy policy|Modern Slavery Act Transparency Statement|Sitemap|About US| Contact US: help@patsnap.com