Manufacturing method of iron-based friction plate
A production method and technology of friction plates, applied in friction linings, mechanical equipment, etc., can solve problems such as strength reduction, failure to meet product technical requirements, warping and deformation, etc., achieve temperature reduction, suitable for mass production, and small deformation Effect
- Summary
- Abstract
- Description
- Claims
- Application Information
AI Technical Summary
Problems solved by technology
Method used
Examples
Embodiment
[0027] The process flow described in the present invention includes the following multiple processes: 1. Ingredients → 2, material mixing → 3, pressing → 4, friction layer sintering → 5, core plate copper plating → 6, medium temperature pressurization compound → 7, oil tank processing.
[0028] Processes 1, 2, 3, and 7 are the same as the traditional process. Process 4: The parameters of the friction layer sintering process are:
[0029] Sintering temperature: 1050°C--1100°C,
[0030] Holding time: 2.5---3.5 hours,
[0031] Atmosphere: Ammonia decomposition gas,
[0032] Equipment: Bell-type pressurized sintering furnace or iron-based through-type continuous sintering furnace;
[0033] Process 5: Copper plating on the core board: Copper-plating the core board by electroplating; hang the core board on the cathode, hang the copper plate on the anode, add the electroplating solution containing copper ions into the electroplating tank, and connect the direct current, according ...
PUM
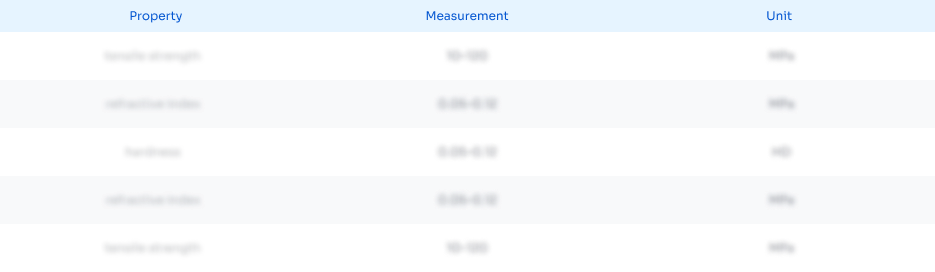
Abstract
Description
Claims
Application Information

- Generate Ideas
- Intellectual Property
- Life Sciences
- Materials
- Tech Scout
- Unparalleled Data Quality
- Higher Quality Content
- 60% Fewer Hallucinations
Browse by: Latest US Patents, China's latest patents, Technical Efficacy Thesaurus, Application Domain, Technology Topic, Popular Technical Reports.
© 2025 PatSnap. All rights reserved.Legal|Privacy policy|Modern Slavery Act Transparency Statement|Sitemap|About US| Contact US: help@patsnap.com