Catalyst for removing NOx in incineration gas and preparation method thereof
A technology for incinerating flue gas and catalysts, which is applied in catalyst activation/preparation, chemical instruments and methods, physical/chemical process catalysts, etc. It can solve the problems of low operating temperature, high cost of precious metal catalysts, and difficulty in popularization and application, and meet equipment requirements. Low, strong anti-toxic ability, easy to prepare and operate
- Summary
- Abstract
- Description
- Claims
- Application Information
AI Technical Summary
Problems solved by technology
Method used
Image
Examples
Embodiment 1
[0028] Ultrasonic disperse 0.5g carbon nanotubes (CNTs) and 0.05g hexadecyltrimethylammonium bromide in ethanol and oscillate ultrasonically to obtain liquid A; dissolve 40ml butyl orthotitanate in 60ml ethanol, then add 9ml of hydrolysis inhibitor acetic acid, and ultrasonically oscillate to obtain liquid B; under the condition of ultrasonic oscillation, dissolve 2.5g of manganese acetate and 1g of cerium nitrate in 20ml of ethanol, then add 8ml of deionized water to obtain liquid C; slowly pour out liquid A Pour into solution B, sonicate for 30 minutes, then pour into solution C, and continue to sonicate until a sol is formed. After the sol was aged at room temperature for 24 hours, it was dried at 80°C, calcined at 500°C for 4 hours under the protection of nitrogen, cooled, and ground to obtain the catalyst. Its energy spectrum is as follows figure 1 As shown, calculated from the corresponding peak areas in the figure: MnO with 7.5wt% CNTs, 9wt% Mn, and 4.5wt% Ce x -CeO 2...
Embodiment 2
[0031] Ultrasonic disperse 0.5g carbon nanotubes (CNTs) and 0.05g hexadecyltrimethylammonium bromide in ethanol, and ultrasonically oscillate to obtain liquid A; dissolve 40ml butyl orthotitanate in 60ml ethanol, and then add 9ml of hydrolysis inhibitor acetic acid was ultrasonicated to obtain liquid B; 2.5g of manganese acetate and 1g of cerium nitrate were dissolved in 20ml of ethanol, and then 10ml of deionized water was added to obtain liquid C. Slowly pour liquid A into liquid B, sonicate for 30 minutes, then pour into liquid C, transfer the mixed solution to a stainless steel hydrothermal reaction kettle with a polytetrafluoroethylene liner, and react at 230°C and a pressure of 45Mpa 3 hours. After suction filtration and washing, dry at 60°C, calcinate at 450°C for 4h under the protection of nitrogen, cool, and grind to obtain MnO with about 7.7wt% CNTs, about 8.8wt% Mn, and about 4.2wt% Ce x -CeO 2 / TiO 2 - CNTs catalyst.
[0032] Get 8ml of the catalyst of the pres...
Embodiment 3
[0034] Ultrasonic dispersion of 0.5g of carbon nanotubes CNTs in water, ultrasonic oscillation, to obtain liquid A; under the condition of ultrasonic oscillation, 2.5g of manganese acetate, 1g of cerium nitrate, 3.2g of titanium sulfate were dissolved in 20ml of ethanol, and then 40ml of deionized water to obtain solution B; under the condition of ultrasonic oscillation, mix the two solutions of A and B, and then add ammonia water dropwise until no precipitation is formed. After suction filtration and washing, dry at 80°C, calcinate at 480°C for 6h under the protection of nitrogen, cool, and grind to obtain MnO with about 7.7wt% CNTs, about 9.5wt% Mn, and about 4.1wt% Ce x -CeO 2 / TiO 2 - CNTs catalyst.
[0035] Get 8ml of the catalyst of the present invention, add 20wt% bentonite and an appropriate amount of water to stir, apply it on the above-mentioned aluminum sheets, insert ten pieces of aluminum sheets into a fixed-bed reactor for catalytic testing, NO X and NH 3 Con...
PUM
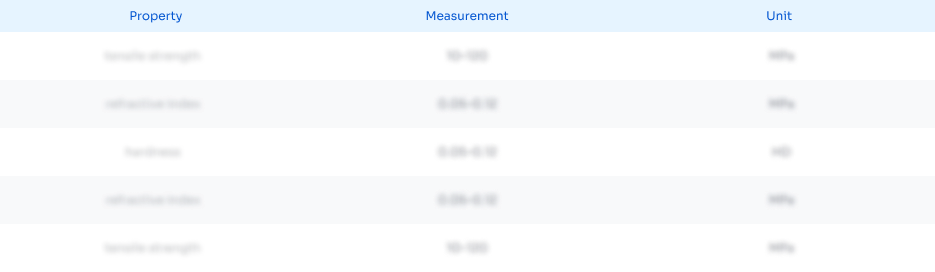
Abstract
Description
Claims
Application Information

- R&D
- Intellectual Property
- Life Sciences
- Materials
- Tech Scout
- Unparalleled Data Quality
- Higher Quality Content
- 60% Fewer Hallucinations
Browse by: Latest US Patents, China's latest patents, Technical Efficacy Thesaurus, Application Domain, Technology Topic, Popular Technical Reports.
© 2025 PatSnap. All rights reserved.Legal|Privacy policy|Modern Slavery Act Transparency Statement|Sitemap|About US| Contact US: help@patsnap.com