Preparation method of tin-zinc composite oxide material with even size and micro-nano structure
A composite oxide and tin-zinc technology, which is applied in nanostructure manufacturing, microstructure technology, microstructure devices, etc., can solve environmental hazards and other problems, and achieve the effects of convenient operation, simple process equipment, and easy industrial production
- Summary
- Abstract
- Description
- Claims
- Application Information
AI Technical Summary
Problems solved by technology
Method used
Image
Examples
Embodiment 1
[0017] Weigh 0.35 g of tin tetrachloride, 0.22 g of zinc acetate and 0.80 g of sodium hydroxide into an agate mortar, mix them evenly, grind for 2 hours, then use alcohol for ultrasonic cleaning and centrifugation for 3 times, and put the powder in a drying oven at 80 ° C After drying, place it in a muffle furnace for calcination for 2 hours, the calcination temperature is 800°C, and the phase obtained after cooling is figure 1 , the shape is figure 2 A mixed powder of zinc stannate and tin oxide.
Embodiment 2
[0019] Weigh 0.35 g of tin tetrachloride, 0.44 g of zinc acetate and 0.80 g of sodium hydroxide into an agate mortar, mix them evenly, grind for 2 hours, then filter and wash them with deionized water twice, and place the powder in a drying oven at 60°C After drying, place it in a muffle furnace for calcination for 2 hours, the calcination temperature is 800°C, and it can be obtained after cooling image 3 Zinc stannate powder.
Embodiment 3
[0021] Weigh 3.5 grams of tin tetrachloride, 4.4 grams of zinc acetate and 10 grams of sodium hydroxide and put them into an agate mortar and mix them evenly, then transfer them to a stainless steel ball mill jar, and ball mill them on a planetary ball mill for 1 hour. After drying the powder in a drying oven at 100°C, place it in a muffle furnace and calcinate for 2 hours at a temperature of 800°C. After cooling, you can get Figure 4 Zinc stannate and zinc oxide mixed powder.
PUM
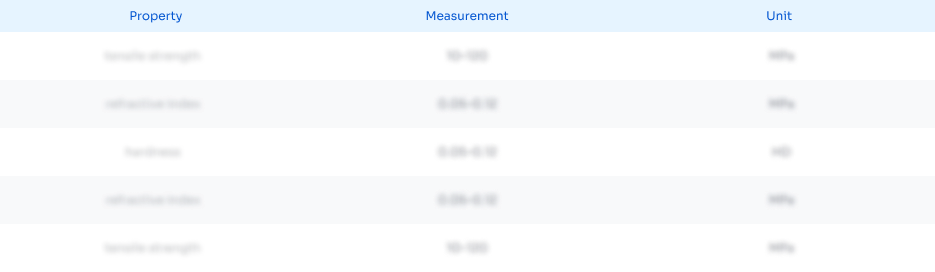
Abstract
Description
Claims
Application Information

- R&D
- Intellectual Property
- Life Sciences
- Materials
- Tech Scout
- Unparalleled Data Quality
- Higher Quality Content
- 60% Fewer Hallucinations
Browse by: Latest US Patents, China's latest patents, Technical Efficacy Thesaurus, Application Domain, Technology Topic, Popular Technical Reports.
© 2025 PatSnap. All rights reserved.Legal|Privacy policy|Modern Slavery Act Transparency Statement|Sitemap|About US| Contact US: help@patsnap.com