Epoxy polyamide resin wet strength agent and preparation method thereof
A technology of epoxy polyamide and wet strength agent, which is applied in the direction of reinforcing agent addition, etc. It can solve the problems of low polymer molecular weight, serious volatilization of raw materials, and affecting the use effect, etc., and achieve high molecular weight distribution, less volatilization loss, and high wet strength. effect of effect
- Summary
- Abstract
- Description
- Claims
- Application Information
AI Technical Summary
Problems solved by technology
Method used
Image
Examples
Embodiment 1
[0022] Add 53.5 grams of dihexamethylenetriamine and 41.5 grams of isophthalic acid to a high-pressure reactor equipped with a stirrer, thermometer, condenser, and nitrogen inlet and outlet, pressurize to 1Mpa with nitrogen, and heat up to 100°C After 3 hours of heat preservation, add 463.8 grams of deionized water with a viscosity of 1250 centipoise (25° C.), which is a bright light yellow transparent viscous odorless liquid.
[0023] When the temperature dropped to 20°C, 23.13 g of epichlorohydrin was added dropwise, and the dropwise addition was completed in 20 minutes. The reaction was continued for 1 hour, and the reaction was stopped. The product was a light yellow viscous liquid.
[0024] The weight solid content is 20.3%, the molecular weight is 172,500, the viscosity is 52 centipoise (25°C), the test method is GB12005.1-89, and the application effect is shown in Attached Table 1 and Attached Table 2.
Embodiment 2
[0026] Add 69 grams of ethylenediamine and 166.13 grams of terephthalic acid to the high-pressure reactor in the same device as in Example 1, pressurize to 2Mpa after stirring evenly, heat up to 150°C, and keep warm for 2.5 hours, then add 1825.5 grams of deionized Water with a viscosity of 1350 centipoise (25°C). It is light yellow transparent viscous odorless liquid.
[0027] When the temperature dropped to 30°C, 138.78 g of epichlorohydrin was added dropwise, and the dropwise addition was completed in 30 minutes. The reaction was continued for 2.5 hours, and the reaction was stopped. The product was a light yellow viscous liquid.
[0028] The weight solid content is 17%, the molecular weight is 174,000, and the viscosity is 105 centipoise (25°C). The test method is the same as above, and the application effect is shown in attached table 1 and attached table 2.
Embodiment 3
[0030] Add 59 grams of guanidine and 90 grams of methyl terephthalate to the high-pressure reactor in the same device as in Example 1, stir evenly and heat up to 130° C. After 2 hours of heat preservation, add 890 grams of deionized water, and the viscosity is 1760 centimeters. Poise (25°C). It is light yellow transparent viscous odorless liquid.
[0031] When the temperature dropped to 35°C, 115 grams of epichlorohydrin was added dropwise, and the dropwise addition was completed in 40 minutes. The reaction was continued for 2 hours, and the reaction was stopped. The product was a light yellow viscous liquid.
[0032] The weight solid content is 22.9%, the molecular weight is 175,600, and the viscosity is 205 centipoise (25°C). The test method is the same as above, and the application effect is shown in Attached Table 1 and Attached Table 2.
PUM
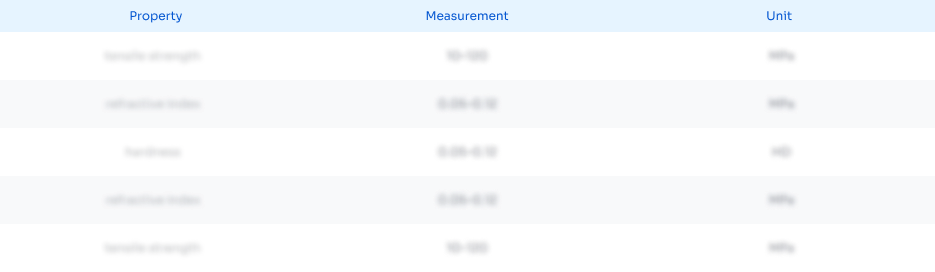
Abstract
Description
Claims
Application Information

- Generate Ideas
- Intellectual Property
- Life Sciences
- Materials
- Tech Scout
- Unparalleled Data Quality
- Higher Quality Content
- 60% Fewer Hallucinations
Browse by: Latest US Patents, China's latest patents, Technical Efficacy Thesaurus, Application Domain, Technology Topic, Popular Technical Reports.
© 2025 PatSnap. All rights reserved.Legal|Privacy policy|Modern Slavery Act Transparency Statement|Sitemap|About US| Contact US: help@patsnap.com