Method for cleanly extracting vanadium pentexide from vanadium containing material
A technology of vanadium pentoxide and substance, applied in vanadium oxide and other directions, can solve the problems of secondary resource waste environment, no industrialization implementation, waste of vanadium ore resources, etc., and achieves short process flow, low production cost, and reduced energy consumption. Effect
- Summary
- Abstract
- Description
- Claims
- Application Information
AI Technical Summary
Problems solved by technology
Method used
Image
Examples
Embodiment 1
[0035] Containing vanadium ore A, its composition is as follows (weight ratio): V 2 o 5 1.2%, SiO 2 76.3%, Al 2 o 3 6.7%, Fe 2 o 3 3.2%, FeO 2.6%, CaO 0.8%, K 1.0%, Na 0.6%, P 2 o 5 0.1%, other 7.5%.
[0036] The vanadium-containing ore A is crushed and wet-ground to 60-80 meshes, 120 kg (dry weight) is added to the standby filtrate 2 returned from the next stage, heated to 90-100° C., reacted for 3.5 hours, and filtered to obtain filtrate 3 and Filter cake 1; filter cake 1 is mixed with standby filtrate 1, heated to 95-100°C, reacted for 2 hours, filtered to obtain standby filtrate 2 and filter cake 2, standby filtrate 2 is used to react with raw ore, filter cake 2 and 6.8 kg Phosphoric acid, 42 kg of sulfuric acid and 100 kg of water were mixed, stirred and reacted at 100°C for 1 hour, filtered to obtain standby filtrate 1 and filter cake 3, filter cake 3 was washed as cement mixture, and standby filtrate 1 was returned to leach filter cake 2 .
[0037] Add 10...
Embodiment 2
[0042] Containing vanadium ore B, its composition is as follows (weight ratio): V 2 o 5 1.6%, SiO 2 16.3%, C 63.8%, Al 2 o 3 7.3%, Fe 2 o 3 1.2%, FeO 4.3%, CaO 0.8%, K 0.3%, Na 0.2%, other 4.2%.
[0043] Vanadium-containing ore B is crushed and wet-ground to 60-80 meshes, 120 kg (dry weight) is added to the standby filtrate 2 returned from the next stage, heated to 85-95°C, reacted for 4.5 hours, and filtered to obtain filtrate 3 and Filter cake 1; filter cake 1 is mixed with standby filtrate 1, heated to 95-100°C, reacted for 3 hours, filtered to obtain standby filtrate 2 and filter cake 2, standby filtrate 2 is used to react with raw ore, filter cake 2 and 8.3 kg Phosphoric acid, 36 kg of sulfuric acid and 100 kg of water were mixed, stirred and reacted at 100°C for 1 hour, filtered to obtain spare filtrate 1 and filter cake 2, filter cake 3 was washed and used as cement mixture, spare filtrate 1 was returned to leaching filter cake 2 .
[0044] Add 11 to 13 kilo...
Embodiment 3
[0049] Industrial waste C, its composition is as follows (weight ratio): V 2 o 5 4.2%, SiO 2 2 6.3%, Al 2 o 3 11.7%, Fe 2 o 3 0.2%, FeO 35.6%, CaO 10.8%, other 3.7%.
[0050] The industrial waste C is crushed and wet-milled to 60-80 mesh, 120 kg (dry weight) is added to the standby filtrate 2 returned from the next stage, heated to 80-90°C, reacted for 2.5 hours, and filtered to obtain filtrate 3 and filtrate Cake 1; filter cake 1 is mixed with standby filtrate 1, heated to 90-95°C, reacted for 1 hour, and filtered to obtain standby filtrate 2 and filter cake 2, standby filtrate 2 is used to react with industrial waste residue, filter cake 2 and 36 kg Phosphoric acid, 96 kg of sulfuric acid and 180 kg of water were mixed, stirred and reacted at 100°C for 0.5 hours, filtered to obtain standby filtrate 1 and filter cake 3, filter cake 3 was washed as cement mixture, and standby filtrate 1 was returned to leach filter cake 2 .
[0051] Add 18-21 kg of ammonium sulfate ...
PUM
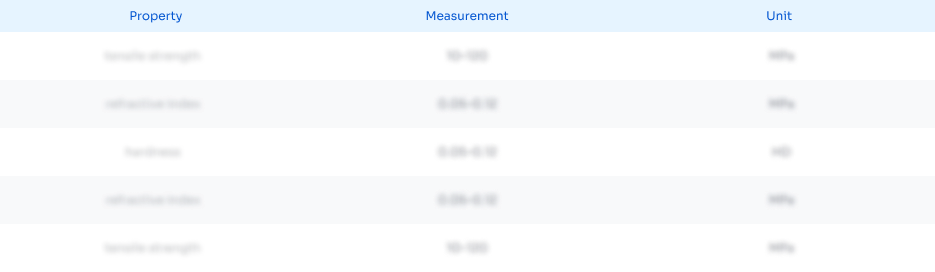
Abstract
Description
Claims
Application Information

- Generate Ideas
- Intellectual Property
- Life Sciences
- Materials
- Tech Scout
- Unparalleled Data Quality
- Higher Quality Content
- 60% Fewer Hallucinations
Browse by: Latest US Patents, China's latest patents, Technical Efficacy Thesaurus, Application Domain, Technology Topic, Popular Technical Reports.
© 2025 PatSnap. All rights reserved.Legal|Privacy policy|Modern Slavery Act Transparency Statement|Sitemap|About US| Contact US: help@patsnap.com