Dithiophosphate composition and utility in rubber
A technology of dithiophosphoric acid and composition, applied in phosphorus organic compounds, compounds of group 5/15 elements of the periodic table, organic chemistry, etc., can solve problems such as toxins
- Summary
- Abstract
- Description
- Claims
- Application Information
AI Technical Summary
Problems solved by technology
Method used
Image
Examples
Embodiment 1
[0029] Example 1: Dithiophosphoric acid, Lot RJT-543-233
[0030] Add 86.2 grams of phosphorus pentasulfide and 100 mL of heptane into the three-necked flask. The flask was connected to a scrubber to remove hydrogen sulfide gas that would form during the reaction. A mixture of 85.1 grams of 2-ethylhexanol, 24.3 grams of n-butanol and 39.0 grams of 1,6-hexanediol was added to the addition funnel. The addition funnel was heated to 44°C to dissolve the 1,6-hexanediol solid in the other two alcohols. The mixture was then added to the phosphorus pentasulfide mixture over 15 minutes. The addition funnel was washed with 20 mL of heptane, which was then added to the reaction mixture. The reaction was gradually heated to 105°C and maintained at this temperature for two and a half hours. The temperature was then raised to 120°C as the heptane was distilled off. The reaction was maintained at 125°C for about four hours. The reaction was then attached to an aspirator to ensure all ...
Embodiment 2
[0031] Example 2: Polymeric dithiophosphate OCD-337, Lot RJT-543-241
[0032] 191.3 grams of dithiophosphoric acid (RJT-543-233) in Example 1 was added to the three-necked flask. This was attached to an addition funnel containing a mixture of water (42.2 g) and 30% hydrogen peroxide (42.1 g, 0.371 moles). The reaction flask was placed in an ice water bath and the hydrogen peroxide solution was added slowly over three hours. The addition funnel was then washed with 40 mL of water and added to the reaction. The reaction temperature was kept below 40°C while hydrogen peroxide was added. The reaction was then heated to 56°C and then allowed to cool back to room temperature. Another 2.5 g of 30% hydrogen peroxide was added. Then stir for about 30 minutes. The product was mixed with 79.6g of Hi- ABS (a solid carrier) was mixed and dried in a 46°C oven to obtain a homogeneous powder.
Embodiment 3
[0033] Example 3: Dithiophosphoric acid for the preparation of OCD-338, Lot RJT-543-244
[0034] 74.1 g of phosphorus pentasulfide and 60.2 g of heptane were added to the three-necked flask. The flask was connected to a scrubber to remove any hydrogen sulfide gas that would form during the reaction. The flask was then placed in an ice water bath. To the addition funnel was added 37.2 grams of dipropylene glycol and 104.4 grams of 2-ethylhexanol. The alcohol mixture was then added to the phosphorus pentasulfide over 15 minutes. The addition funnel was rinsed with 20 mL of heptane and added to the reaction flask. The reaction was slowly heated to 115°C and the heptane was distilled off. The reaction was heated at 115 °C for 4.5 hours and then attached to an aspirator to remove any residual solvent. After another 30 minutes, the aspirator was removed and the product was filtered through celite.
PUM
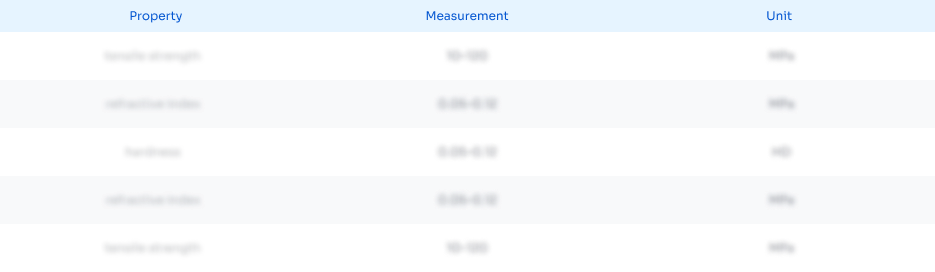
Abstract
Description
Claims
Application Information

- Generate Ideas
- Intellectual Property
- Life Sciences
- Materials
- Tech Scout
- Unparalleled Data Quality
- Higher Quality Content
- 60% Fewer Hallucinations
Browse by: Latest US Patents, China's latest patents, Technical Efficacy Thesaurus, Application Domain, Technology Topic, Popular Technical Reports.
© 2025 PatSnap. All rights reserved.Legal|Privacy policy|Modern Slavery Act Transparency Statement|Sitemap|About US| Contact US: help@patsnap.com