Drying process and drying system for material containing low-boiling point, inflammable and explosive organic solvent
A flammable, explosive, organic solvent technology, applied in the direction of drying solid materials, non-progressive dryers, heating to dry solid materials, etc., can solve the problem of insufficient solvent recovery, low solvent recovery rate, pipeline blockage, etc. To avoid solvent loss and environmental pollution, improve solvent recovery rate, and reduce large flow erosion
- Summary
- Abstract
- Description
- Claims
- Application Information
AI Technical Summary
Problems solved by technology
Method used
Image
Examples
Embodiment 1
[0035] with granularity as Zinc oxide, which contains 50% methanol as raw material, is dried and solvent recovered.
[0036] The zinc oxide wet material enters the dryer 2 at a rate of 10Kg / h, and the drying temperature is 105-110°C. After a residence time of 50-60 minutes, the dried zinc oxide material enters the following condenser 3 for cooling to 20 -25°C discharge, the bottom is filled with an appropriate amount of inert gas for protection. During the whole drying process, the vacuum degree is kept between 0.02-0.03Mpa by controlling the power of jet pump 7 . The solvent recovery rate is 99.5%, and the solvent content in the dried material is 0.5%. No blockage of the pipeline was found, and the solvent only carried a small amount of dust, which was recovered after passing through the spray tower.
[0037] It can be seen from experiments that the method significantly improves the solvent recovery rate and avoids solvent loss and environmental pollution. The amount of ...
Embodiment 2
[0039] Coal powder with a particle size of 0.05-400 μm containing 40% tetrahydrofuran is used as raw material for drying and solvent recovery.
[0040] The pulverized coal material enters the dryer 2 at an amount of 10Kg / h, and the drying temperature is 200-210°C. After a residence time of 55-60 minutes, the pulverized coal material enters the following condenser 3 for cooling to 20-20- The material is discharged at 25°C, and the bottom is filled with an appropriate amount of inert gas for protection. During the whole drying process, the vacuum degree is kept between 0.03-0.04 MPa by controlling the power of the jet pump 7 . After testing, the solvent content in the coal powder after drying is 0.4%, and the solvent recovery rate reaches 99.6%. No blockage of the pipeline was found, and the solvent only carried a small amount of dust, which was recovered after passing through the spray tower.
Embodiment 3
[0042] Use ordinary medium-temperature asphalt and 50% quinoline as raw materials for drying and solvent recovery. This kind of material has a relatively high viscosity during the drying process. With the ordinary drying process, the solvent recovery is relatively low, less than 90%. Spontaneous combustion, safety accidents occur, and cause environmental pollution. Adopting the process of the present invention, the wet material of ordinary medium-temperature asphalt containing 50% quinoline enters the dryer 2 at an amount of 10Kg / h, and the drying temperature is 280-285°C. After a residence time of 100 minutes, the medium-temperature after drying The bitumen enters the following condenser 3 to be cooled to 20-25°C and discharged, and the bottom is filled with an appropriate amount of inert gas for protection. During the whole drying process, the vacuum degree is kept between 0.4-0.5 MPa by controlling the power of the jet pump 7 . The solvent recovery rate is 99.8%, and the ...
PUM
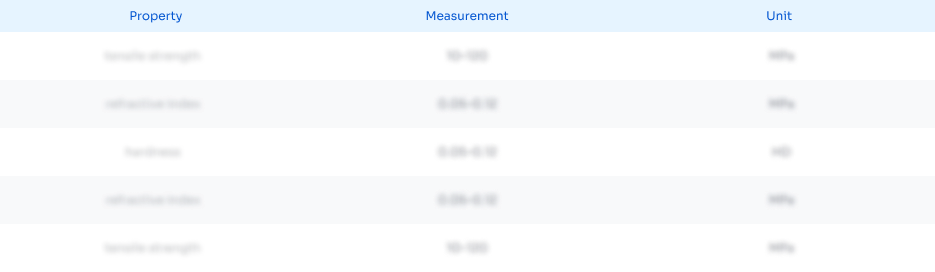
Abstract
Description
Claims
Application Information

- R&D
- Intellectual Property
- Life Sciences
- Materials
- Tech Scout
- Unparalleled Data Quality
- Higher Quality Content
- 60% Fewer Hallucinations
Browse by: Latest US Patents, China's latest patents, Technical Efficacy Thesaurus, Application Domain, Technology Topic, Popular Technical Reports.
© 2025 PatSnap. All rights reserved.Legal|Privacy policy|Modern Slavery Act Transparency Statement|Sitemap|About US| Contact US: help@patsnap.com