Method for preparing surface-modified proppant
A technology of surface modification and surfactant, which is applied in chemical instruments and methods, earthwork drilling, and drilling compositions, etc. It can solve the problems of easy detachment of the hydrophobic film on the surface of the proppant and unstable corrosion resistance of the proppant. , to achieve the effect of excellent thickening, stability and corrosion resistance
- Summary
- Abstract
- Description
- Claims
- Application Information
AI Technical Summary
Problems solved by technology
Method used
Examples
Embodiment 1
[0025] Heat 10kg of quartz sand 20 / 40 mesh to 300°C, put it into a sand mixer, stir and then cool down to 200°C. Add 1 kg of phenolic resin to the heated quartz sand and stir evenly to form a mixture, then add 0.01 kg of polyether dimethyl siloxane and 0.2 kg of hexamethylenetetramine and stir evenly. When the phenolic resin-quartz sand mixture starts to agglomerate, add 0.05kg calcium stearate and 0.02kg polydimethylsiloxane and stir evenly. The obtained mixture is cooled, crushed and sieved to obtain proppant S1.
[0026] In this embodiment, the purpose of heating is to provide a certain reaction temperature for the next step. In actual operation, the substrate can be heated to a higher temperature, such as 150-300°C, and then cooled to 100-240°C. The purpose of this is to remove the volatile impurities on the surface of the substrate raw material to ensure the subsequent coating. The bond between the resin material and the matrix material is tighter, and at the same time,...
Embodiment 2
[0029]Heat 10kg of ceramsite sand 20 / 40 mesh to 260°C, put it into a sand mixer and stir it, then cool it down to 100°C. Add 0.2kg of furan resin to the heated ceramsite sand and stir evenly to form a mixture, then add 0.01kg of polyether methyl hydrogen siloxane, 0.04kg of dibutyl phthalate, and then add 0.02kg of benzenesulfonic acid , toluenesulfonic acid mixture and stir well. Add 0.004kg of ethylene bisstearic acid amide and 0.02kg of polymethylhydrogensiloxane before the furan resin-ceramic sand mixture starts to agglomerate and stir evenly. The obtained mixture is cooled, crushed and sieved to obtain proppant S2.
[0030] The role of dibutyl phthalate as a plasticizer is to improve the performance of the resin film, reduce its brittleness and increase its resistance to crushing.
Embodiment 3
[0032] Heat 10kg of quartz sand 20 / 40 mesh and ceramsite sand 20 / 40 mesh mixture to 300°C, put it into a sand mixer and stir it, then cool it down to 240°C. Add 1.5kg furan resin to the heated mixture of quartz sand and ceramsite sand and stir evenly to form a mixture, then add 0.003kg polyhydroxyvinyl methyl hydrogen siloxane, 0.045kg diisooctyl phthalate , then add 0.045kg xylenesulfonic acid and stir evenly. Add the mixture of 0.15kg polyethylene wax and oxidized polyethylene wax, 0.006kg polymethylhydrogensiloxane and stir evenly before the mixture of furan resin-quartz sand and ceramsite sand starts to agglomerate. The obtained mixture is cooled, crushed and sieved to obtain proppant S3.
PUM
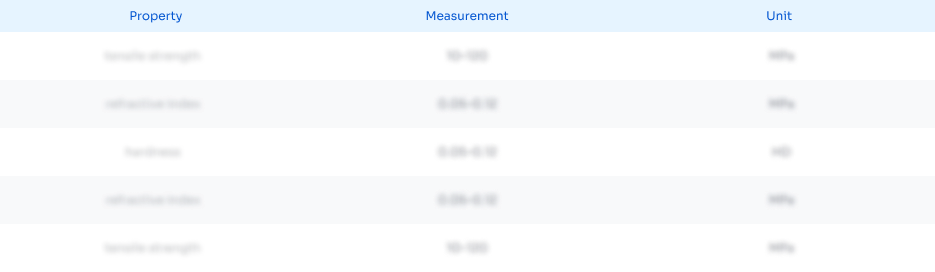
Abstract
Description
Claims
Application Information

- R&D Engineer
- R&D Manager
- IP Professional
- Industry Leading Data Capabilities
- Powerful AI technology
- Patent DNA Extraction
Browse by: Latest US Patents, China's latest patents, Technical Efficacy Thesaurus, Application Domain, Technology Topic, Popular Technical Reports.
© 2024 PatSnap. All rights reserved.Legal|Privacy policy|Modern Slavery Act Transparency Statement|Sitemap|About US| Contact US: help@patsnap.com