Method for manufacturing large-diameter silicon wafer
A manufacturing method and large-diameter technology, applied in semiconductor/solid-state device manufacturing, electrical components, circuits, etc., can solve problems affecting processing speed, etc., achieve the effects of increasing productivity, reducing polishing time, and ensuring processing accuracy
- Summary
- Abstract
- Description
- Claims
- Application Information
AI Technical Summary
Problems solved by technology
Method used
Image
Examples
Embodiment 1
[0023] Use 30 12-inch slices of P (100) produced by the Czochralski method, grind the silicon wafer with a double-sided grinding machine, and use the AFS3220 geometric parameter tester to test the silicon wafer GBIR (the total thickness change of the silicon wafer) after grinding. To measure, the GBIR value of each piece is as figure 2 shown. It can be seen from the figure that the GBIR is less than 1 micron, with an average value of 0.839 micron.
Embodiment 2
[0025] Get the above 30 silicon wafers through double-sided grinding, and use the method of the present invention to carry out double-sided polishing on a Speedfam20B polishing machine, and the polishing removal amount is 30 microns. Then wash it with a washing machine and dry it with a spin dryer. See GBIR after polishing. image 3 . It can be seen from the figure that the precision of the present invention is high, and the average value of GBIR is 0.459 microns, which are all less than 0.6 microns.
PUM
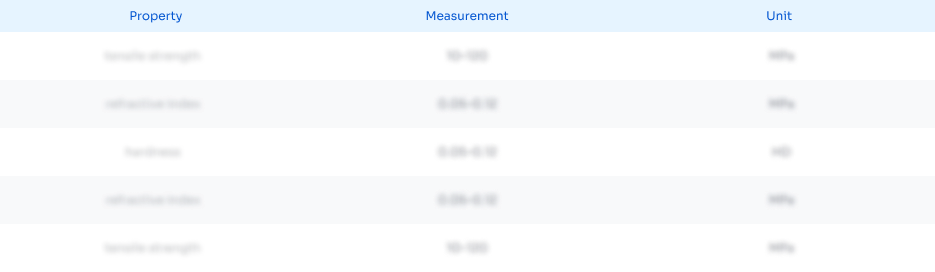
Abstract
Description
Claims
Application Information

- R&D
- Intellectual Property
- Life Sciences
- Materials
- Tech Scout
- Unparalleled Data Quality
- Higher Quality Content
- 60% Fewer Hallucinations
Browse by: Latest US Patents, China's latest patents, Technical Efficacy Thesaurus, Application Domain, Technology Topic, Popular Technical Reports.
© 2025 PatSnap. All rights reserved.Legal|Privacy policy|Modern Slavery Act Transparency Statement|Sitemap|About US| Contact US: help@patsnap.com