Method for preparing porzite powder by fly ash
A technology of mullite powder and fly ash, which is applied in the field of synthesizing high-temperature ceramic materials, can solve the problems of expensive organic raw materials, low conversion rate of mullite, and harsh synthesis conditions, so as to be beneficial to environmental protection and save minerals Resources and energy, the effect of low preparation temperature
- Summary
- Abstract
- Description
- Claims
- Application Information
AI Technical Summary
Problems solved by technology
Method used
Examples
Embodiment 1
[0012] Embodiment 1: First, put the fly ash and bauxite raw materials into a ball mill for dry grinding respectively, use alumina ball stone as the grinding medium, control the mass ratio of the ball and the raw material to be 2:1, grind for 3 hours respectively, and then After passing through a 120-mesh sieve, use permanent magnets to remove iron twice, and then use electromagnetic iron to remove iron twice to make the Fe in fly ash and bauxite 2 o 3 The content is lower than 0.5%; secondly, take the above-mentioned fly ash and bauxite after iron removal treatment and put them into alumina crucibles respectively, and place the alumina crucibles in a silicon carbide rod resistance furnace at a temperature of 5 ° C / The heating rate of min is raised to 200°C, kept for 3 hours, and taken out after natural cooling; finally, the naturally cooled fly ash and bauxite are poured into the material at a mass ratio of fly ash: bauxite = 1: 1.2 and stirred Stir evenly in the container,...
Embodiment 2
[0013] Embodiment 2: First, put the fly ash and the bauxite raw material into the ball mill for dry grinding respectively, utilize alumina ball stone as the grinding medium, control the mass ratio of the ball and the raw material to be 3: 1, and grind for 0.5h respectively, After passing through a 120-mesh sieve, permanent magnets were used to remove iron twice, and then electromagnetic iron removal was used to make Fe in fly ash and bauxite twice. 2 o 3 The content is lower than 0.5%; secondly, take the above-mentioned fly ash and bauxite after iron removal treatment and put them into alumina crucibles respectively, and place the alumina crucibles in a silicon carbide rod resistance furnace at a temperature of 5 ° C / The heating rate of min is raised to 400°C, kept for 1 hour, and taken out after natural cooling; finally, the naturally cooled fly ash and bauxite are poured into the material at a mass ratio of fly ash: bauxite = 1: 0.15 and stirred Stir evenly in the contain...
Embodiment 3
[0014] Embodiment 3: First, put the fly ash and bauxite raw materials into a ball mill for dry grinding respectively, use alumina ball stone as the grinding medium, control the mass ratio of the ball and the raw material to be 2.5:1, grind for 2 hours respectively, and then After passing through a 120-mesh sieve, use permanent magnets to remove iron twice, and then use electromagnetic iron to remove iron twice to make the Fe in fly ash and bauxite 2 o 3 The content is lower than 0.5%; secondly, take the above-mentioned fly ash and bauxite after iron removal treatment and put them into alumina crucibles respectively, and place the alumina crucibles in a silicon carbide rod resistance furnace at a temperature of 5 ° C / The heating rate of min is raised to 300°C, kept for 2 hours, and taken out after natural cooling; finally, the naturally cooled fly ash and bauxite are poured into the material at a mass ratio of fly ash: bauxite = 1:3 and stirred Stir evenly in the container, ...
PUM
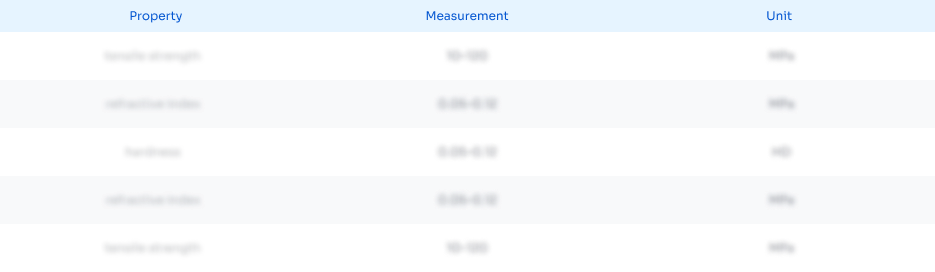
Abstract
Description
Claims
Application Information

- R&D
- Intellectual Property
- Life Sciences
- Materials
- Tech Scout
- Unparalleled Data Quality
- Higher Quality Content
- 60% Fewer Hallucinations
Browse by: Latest US Patents, China's latest patents, Technical Efficacy Thesaurus, Application Domain, Technology Topic, Popular Technical Reports.
© 2025 PatSnap. All rights reserved.Legal|Privacy policy|Modern Slavery Act Transparency Statement|Sitemap|About US| Contact US: help@patsnap.com