Method for preparing tungsten carbide abrasion resistant composite coating by penetration brazing method
A composite coating, tungsten carbide technology, used in welding equipment, manufacturing tools, metal processing equipment, etc., can solve the problems of low bonding strength and thin metal protective coating thickness, restore mechanical properties, reduce the number of shutdowns for maintenance, temperature uniformity
- Summary
- Abstract
- Description
- Claims
- Application Information
AI Technical Summary
Problems solved by technology
Method used
Examples
Embodiment 1
[0025] The method for the tungsten carbide wear-resistant composite coating prepared by the infiltration brazing method described in the present embodiment: comprises the following steps:
[0026] (1) Paste the coated metal powder cloth containing tungsten carbide-cobalt (WC-Co), nickel (Ni), chromium (Cr) mixed powder on the metal substrate with epoxy resin adhesive;
[0027] (2), BNi-2 brazing material is prepared into solder metal powder cloth and pasted on the coated metal powder cloth of step (1);
[0028] (3) Infiltration brazing is carried out in a vacuum furnace. During brazing, the first stage of heating removes the forming agent and binder in the metal cloth, and the second stage of heating melts the solder and penetrates into the coated cloth to remove the tungsten carbide Joining together to form a coating, the solder simultaneously diffuses into the base metal to join the coating and base metal together, forming a metallurgically bonded interface.
[0029] In the...
Embodiment 2
[0039] The method for the tungsten carbide wear-resistant composite coating prepared by the infiltration brazing method described in the present embodiment: comprises the following steps:
[0040] (1) Paste the coated metal powder cloth containing tungsten carbide-cobalt (WC-Co), nickel (Ni), chromium (Cr) mixed powder on the metal substrate with epoxy resin adhesive;
[0041] (2), BNi-2 brazing material is prepared into solder metal powder cloth and pasted on the coated metal powder cloth of step (1);
[0042] (3) Infiltration brazing is carried out in a vacuum furnace. During brazing, the first stage of heating removes the forming agent and binder in the metal cloth, and the second stage of heating melts the solder and penetrates into the coated cloth to remove the tungsten carbide Joining together to form a coating, the solder simultaneously diffuses into the base metal to join the coating and base metal together, forming a metallurgically bonded interface.
[0043]In the ...
Embodiment 3
[0053] The method for the tungsten carbide wear-resistant composite coating prepared by the infiltration brazing method described in the present embodiment: comprises the following steps:
[0054] (1) Paste the coated metal powder cloth containing tungsten carbide-cobalt (WC-Co), nickel (Ni), chromium (Cr) mixed powder on the metal substrate with epoxy resin adhesive;
[0055] (2), BNi-2 brazing material is prepared into solder metal powder cloth and pasted on the coated metal powder cloth of step (1);
[0056] (3) Infiltration brazing is carried out in a vacuum furnace. During brazing, the first stage of heating removes the forming agent and binder in the metal cloth, and the second stage of heating melts the solder and penetrates into the coated cloth to remove the tungsten carbide Joining together to form a coating, the solder simultaneously diffuses into the base metal to join the coating and base metal together, forming a metallurgically bonded interface.
[0057] In the...
PUM
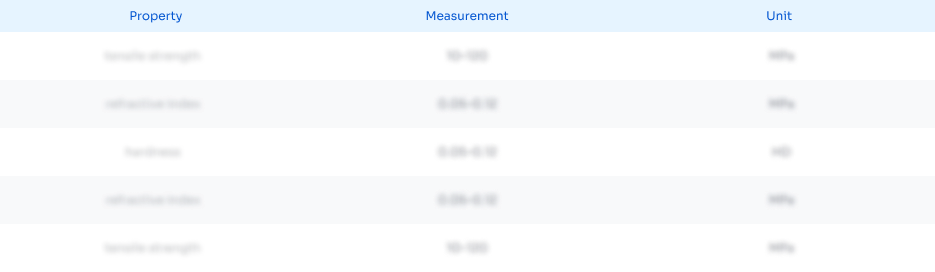
Abstract
Description
Claims
Application Information

- R&D
- Intellectual Property
- Life Sciences
- Materials
- Tech Scout
- Unparalleled Data Quality
- Higher Quality Content
- 60% Fewer Hallucinations
Browse by: Latest US Patents, China's latest patents, Technical Efficacy Thesaurus, Application Domain, Technology Topic, Popular Technical Reports.
© 2025 PatSnap. All rights reserved.Legal|Privacy policy|Modern Slavery Act Transparency Statement|Sitemap|About US| Contact US: help@patsnap.com