Diamond grinding wheel for cutting silicon crystal circle and preparation method thereof
A diamond grinding wheel and silicon wafer technology, which is applied in metal processing equipment, manufacturing tools, grinding/polishing equipment, etc., can solve the problems that the grinding wheel cannot guarantee the strength and rigidity, affects the cutting quality and cutting efficiency, and chipping, and achieves Reduced processing time, good strength and rigidity, reduced chipping and serpentine cutting effects
- Summary
- Abstract
- Description
- Claims
- Application Information
AI Technical Summary
Problems solved by technology
Method used
Image
Examples
Embodiment 1
[0036] (1) Selection of raw materials and their technical conditions:
[0037] Nickel sulfate: chemically pure, the content of nickel sulfate hexahydrate is more than 99.5%;
[0038] Cobalt sulfate: chemically pure, the content of cobalt sulfate heptahydrate is above 99.5%;
[0039] Diamond powder: the particle size is from 320# to 4800#, and the quality reaches the national standard;
[0040] Deionized water: pH value: 6.5~7.5; conductivity: below 5.0μs / cm;
[0041] Aluminum alloy substrate: grade 7050;
[0042] Suspending agent: nonylphenol polyoxyethylene ether (OP-10).
[0043] The above-mentioned raw materials are commonly used component materials in the art, and are known substances well known to those skilled in the art;
[0044] Raw material pretreatment:
[0045] Diamond powder pretreatment:
[0046] ① Treat the selected diamond powder with 50% (volume percent) nitric acid at 80°C for 2 hours for demagnetization and decontamination;
[0047] ② Wash 3 times with...
Embodiment 2
[0067]An ultra-thin, 0.015 mm, ultra-fine, ±0.002 mm, roulette-type diamond grinding wheel was prepared by the method in Example 1.
[0068] Take ordinary ultra-thin, 0.015mm, ultra-fine, ±0.002mm, flat cutting grinding wheel.
[0069] Use the above two grinding wheels to cut silicon wafers respectively. The disc type grinding wheel obtained in Example 1 greatly reduces the chipping and serpentine cutting of the product, reduces the occurrence of damage, fracture, etc., thereby improving the cutting accuracy and shortening the cutting time. The processing time is reduced, and the production efficiency is increased by about 15%.
PUM
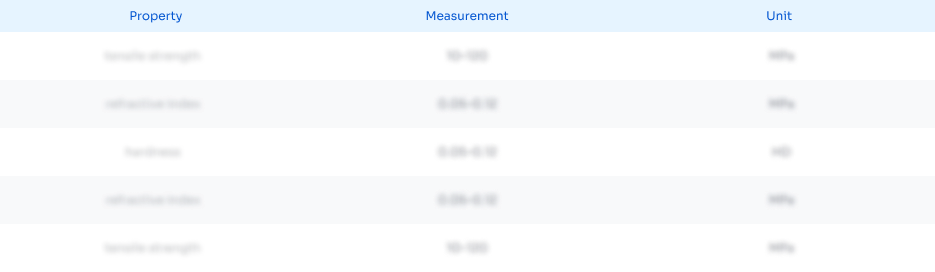
Abstract
Description
Claims
Application Information

- R&D
- Intellectual Property
- Life Sciences
- Materials
- Tech Scout
- Unparalleled Data Quality
- Higher Quality Content
- 60% Fewer Hallucinations
Browse by: Latest US Patents, China's latest patents, Technical Efficacy Thesaurus, Application Domain, Technology Topic, Popular Technical Reports.
© 2025 PatSnap. All rights reserved.Legal|Privacy policy|Modern Slavery Act Transparency Statement|Sitemap|About US| Contact US: help@patsnap.com