Low-vanadium denitration catalyst and preparation method and application thereof
A denitration catalyst, catalyst technology, applied in catalyst activation/preparation, chemical instruments and methods, physical/chemical process catalysts, etc., can solve the problems of pollution, high catalyst cost, and high toxicity of precursors, and achieve the effect of improving performance
- Summary
- Abstract
- Description
- Claims
- Application Information
AI Technical Summary
Problems solved by technology
Method used
Image
Examples
Embodiment 1
[0018] Example 1: 0.1 wt% V 2 o 5 -6wt% WO 3 -1wt%CeO 2 / TiO 2 Preparation of Composite Metal Oxide Catalysts
[0019] a) Add 0.5g of oxalic acid into 20mL of deionized water, stir to dissolve, then add 0.0064g of ammonium metavanadate and 0.3379g of ammonium paratungstate in turn, heat and stir in a water bath at 40°C for 10 minutes, and form a transparent solution
[0020] b) dissolving 0.1261g of cerium nitrate in oxalic acid solution to form a solution, and then adding dropwise into the solution prepared in step a) to form a flocculent precipitate, heating and stirring in a water bath at 40°C for 30 minutes;
[0021] c) Then slowly add 4.645g of titanium dioxide powder to the solution in step b), and add a small amount of deionized water appropriately, and stir evenly for 1 hour to obtain a white slurry;
[0022] d) Put the slurry obtained in step c) into an ultrasonic cleaning machine and ultrasonically impregnate it for 2 hours, then dry it in an oven at 110°C for 1...
Embodiment 2
[0024] Example 2: 0.1 wt% V 2 o 5 -6wt% WO 3 -5wt%CeO 2 / TiO 2 Preparation of Composite Metal Oxide Catalysts
[0025] a) Add 0.5g of oxalic acid to 20mL of deionized water, stir to dissolve, then add 0.0064g of ammonium metavanadate and 0.3379g of ammonium paratungstate in turn, and heat and stir in a water bath at 40°C for 10 minutes to form a transparent solution
[0026] b) dissolving 0.6307g of cerium nitrate in the oxalic acid solution to form a solution, and then adding dropwise into the solution prepared in step a) to form a flocculent precipitate, heating and stirring in a water bath at 40°C for 30 minutes;
[0027] c) Then slowly add 4.445g of titanium dioxide powder to the solution in step b), and add a small amount of deionized water appropriately, and stir evenly for 1 hour to obtain a white slurry;
[0028] d) Put the slurry obtained in step c) into an ultrasonic cleaning machine and ultrasonically impregnate it for 2 hours, then dry it in an oven at 110°C for...
Embodiment 3
[0030] Example 3: 0.1 wt% V 2 o 5 -6wt% WO 3 -10wt%CeO 2 / TiO 2 Preparation of Composite Metal Oxide Catalysts
[0031] a) Add 0.5g of oxalic acid into 20mL of deionized water, stir to dissolve, then add 0.0064g of ammonium metavanadate and 0.3379g of ammonium paratungstate in turn, heat and stir in a water bath at 40°C for 10 minutes, and form a transparent solution
[0032] b) dissolving 1.2614g of cerium nitrate in oxalic acid solution to form a solution, and then adding dropwise to the solution prepared in step a) to form a flocculent precipitate, heating and stirring in a water bath at 40°C for 30 minutes;
[0033] c) Then slowly add 4.195g of titanium dioxide powder to the solution in step b), and add a small amount of deionized water appropriately, and stir evenly for 1 hour to obtain a white slurry;
[0034] d) Put the slurry obtained in step c) into an ultrasonic cleaning machine and ultrasonically impregnate it for 2 hours, then dry it in an oven at 110°C for 12...
PUM
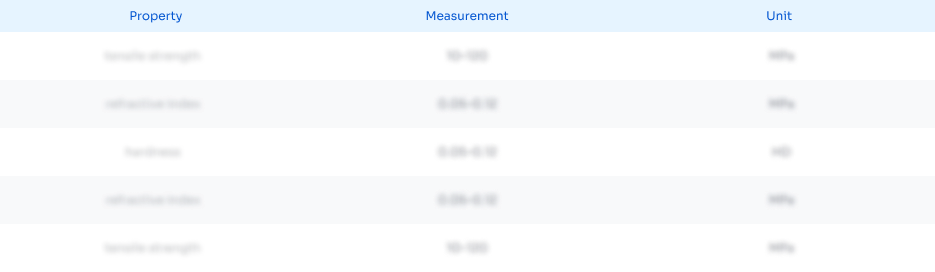
Abstract
Description
Claims
Application Information

- R&D
- Intellectual Property
- Life Sciences
- Materials
- Tech Scout
- Unparalleled Data Quality
- Higher Quality Content
- 60% Fewer Hallucinations
Browse by: Latest US Patents, China's latest patents, Technical Efficacy Thesaurus, Application Domain, Technology Topic, Popular Technical Reports.
© 2025 PatSnap. All rights reserved.Legal|Privacy policy|Modern Slavery Act Transparency Statement|Sitemap|About US| Contact US: help@patsnap.com