Microwave heating plate and chamber and method for manufacturing same
A microwave heating cavity and microwave heating technology, applied in microwave heating and other directions, can solve the problems of easy breakage of resistance wire, silicon carbon rod, silicon molybdenum rod, small heating area of heating element, and low microwave heating efficiency, and achieve significant economic benefits , Low manufacturing cost, outstanding energy-saving effect
- Summary
- Abstract
- Description
- Claims
- Application Information
AI Technical Summary
Problems solved by technology
Method used
Examples
Embodiment 1
[0018] Example 1: Take 30kg of SiC micropowder (about 100 μm in particle size) and 12kg of zirconium-containing aluminum silicate fibers (about 2 to 3 μm in diameter and about 20 to 80 mm in length), add 6kg of sodium silicate, 0.3kg of polyacrylamide, and 1.7kg of Silica powder and appropriate amount of water, fully manual or mechanical mixing, pulping, and then use mechanical extrusion mold molding method to produce the required size and shape of the heating plate or heating cavity - wet billet, and then the heating plate wet billet Or the wet billet in the heating chamber is dried at 150°C for more than 12 hours to ensure sufficient dehydration, and then pre-fired at 1000°C for 2 hours to obtain the finished microwave heating plate or microwave heating chamber of the present invention. The above-mentioned drying and pre-calcination treatment is preferably microwave heating.
Embodiment 2
[0019] Example 2: Take 35kg of SiC micropowder (about 200 μm in particle size) and 8kg of polycrystalline alumina fiber (about 1 to 3 μm in diameter, about 20 to 80 mm in length), add 5kg of sodium silicate, 0.2kg of polyacrylamide, and 1.8kg of clay Fine powder and appropriate amount of water, fully manual or mechanical mixing, pulping, and then use mechanical extrusion mold forming method to produce the required size and shape of the heating plate or heating cavity - wet billet, and then the heating plate wet billet or The wet billet in the heating chamber is dried at 120°C for more than 24 hours to ensure sufficient dehydration, and then pre-fired at 1200°C for 2 hours to obtain the finished microwave heating plate or microwave heating chamber of the present invention. The above-mentioned drying and pre-calcination treatment is preferably microwave heating.
Embodiment 3
[0020] Example 3: Take 25kg of SiC micropowder (about 100 μm in particle size) and 15kg of zirconium-containing aluminum silicate fiber (about 2 to 3 μm in diameter, about 20 to 80 mm in length), add 8kg of sodium silicate, 0.2kg of polyacrylamide, and 1.8kg of Clay fine powder and appropriate amount of water, fully manual or mechanical mixing, pulping, and then use mechanical extrusion mold forming method to produce the required size and shape of the heating plate or heating cavity - wet billet, and then the heating plate wet billet Or the wet billet in the heating chamber is dried at 200°C for more than 12 hours to ensure sufficient dehydration, and then pre-fired at 1200°C for 2 hours to obtain the finished microwave heating plate or microwave heating chamber of the present invention. The above-mentioned drying and pre-calcination treatment is preferably microwave heating.
PUM
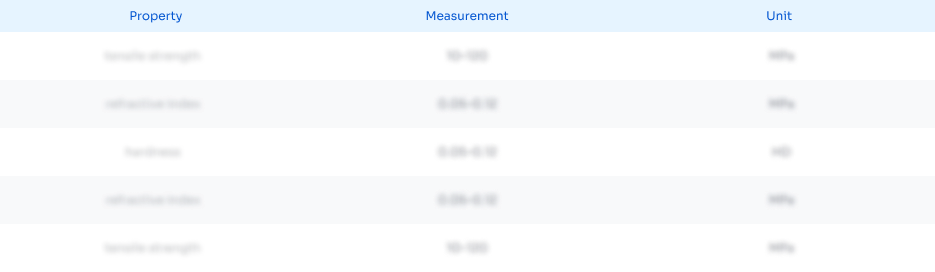
Abstract
Description
Claims
Application Information

- Generate Ideas
- Intellectual Property
- Life Sciences
- Materials
- Tech Scout
- Unparalleled Data Quality
- Higher Quality Content
- 60% Fewer Hallucinations
Browse by: Latest US Patents, China's latest patents, Technical Efficacy Thesaurus, Application Domain, Technology Topic, Popular Technical Reports.
© 2025 PatSnap. All rights reserved.Legal|Privacy policy|Modern Slavery Act Transparency Statement|Sitemap|About US| Contact US: help@patsnap.com