Ceramic fiber fabric-reinforced microwave heating plate and chamber and manufacturing method thereof
A technology of microwave heating cavity and ceramic fiber, which is applied in the direction of microwave heating, etc., can solve the problems of easy breakage of resistance wire, silicon carbon rod, silicon molybdenum rod, small heating area of heating element, and low microwave heating efficiency, and achieve significant economic benefits , Low manufacturing cost, outstanding energy-saving effect
- Summary
- Abstract
- Description
- Claims
- Application Information
AI Technical Summary
Problems solved by technology
Method used
Examples
Embodiment 1
[0026] Embodiment 1: get 9.5kg SiC micropowder (about 100 μm of particle diameter), 0.4kg sodium silicate and 0.1kg cyclohexanone, they carry out mechanical stirring mixing together with water and make slurry A; Get 5kg SiC micropowder (particle diameter about 100μm) and 5kg of sodium silicate, and they were mechanically stirred and mixed with water to prepare slurry B; then the zirconium-containing aluminum silicate fiber fabric pre-fired at 300°C was immersed in slurry A, and at the same time, the slurry was applied The pressure of 10MPa; then use the mold to artificially press the zirconium-containing aluminum silicate fiber fabric after the suction and impregnation treatment to obtain plates of different sizes or cavities of different shapes, and then mold the formed plates and cavities Carry out drying and dehydration treatment at 150°C and curing treatment at 500°C; repeat the above-mentioned slurry suction and impregnation treatment and drying and curing treatment twice ...
Embodiment 2
[0027]Example 2: Get 9kg SiC micropowder (about 150 μm in particle size), 0.9kg silica sol and 0.1kg nonionic octylphenoxyethanol, and carry out mechanical stirring and mixing with water to prepare slurry C; take 5kg SiC micropowder (particle size about 80μm) and 5kg of silica sol, mechanically stir and mix them with water to prepare slurry D; then immerse the pre-fired quartz fiber fabric at 500°C in slurry C, supplemented by a vacuum of 0.01MPa Ultrasonic vibration with conditions and power of 1kW, and then use the mold to mechanically pressurize the quartz fiber fabric after slurry suction and impregnation treatment (pressure is 2MPa) to obtain plates of different sizes or cavities of different shapes, and then shape The finished plate and cavity are subjected to drying and dehydration treatment at 150°C and curing treatment at 600°C; repeat the above slurry suction and impregnation treatment and drying and curing treatment twice (slurry D is used for the last slurry suction...
Embodiment 3
[0028] Embodiment 3: Get 9.2kg SiC micropowder (particle size is about 80 μm), 0.75kg sodium silicate and 0.05kg nonionic octylphenoxyethanol, carry out mechanical stirring and mixing together with water to make slurry; then 400 The pre-fired zirconium-containing aluminum silicate fiber fabric is immersed in the slurry, supplemented by a vacuum condition of 0.01MPa and an ultrasonic vibration with a power of 800W, and then the zirconium-containing aluminum silicate fiber is impregnated with the slurry by using a mold. The fabric is mechanically pressurized (3MPa) to obtain plates of different sizes or cavities of different shapes, and then the formed plates and cavities are dried and dehydrated at 200°C, and finally the prepared plates and cavities are The body was calcined at 1200° C. for 1 hour to finally obtain the ceramic fiber fabric-reinforced microwave heating plate and the finished heating chamber of the present invention.
PUM
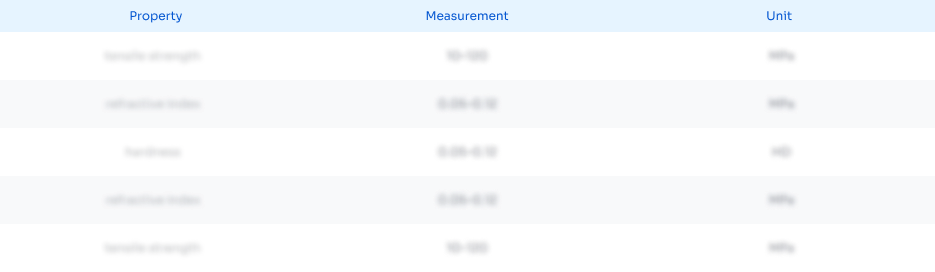
Abstract
Description
Claims
Application Information

- Generate Ideas
- Intellectual Property
- Life Sciences
- Materials
- Tech Scout
- Unparalleled Data Quality
- Higher Quality Content
- 60% Fewer Hallucinations
Browse by: Latest US Patents, China's latest patents, Technical Efficacy Thesaurus, Application Domain, Technology Topic, Popular Technical Reports.
© 2025 PatSnap. All rights reserved.Legal|Privacy policy|Modern Slavery Act Transparency Statement|Sitemap|About US| Contact US: help@patsnap.com