Method for recycling industrial waste sulfate slag
A technology for recycling and processing sulfuric acid residues, which is used in the recycling and processing of sulfuric acid residues, and the use of industrial waste acid to recover and treat sulfuric acid residues. problems, to achieve the effect of improving iron grade and metal recovery rate, saving input, and eliminating the grinding process
- Summary
- Abstract
- Description
- Claims
- Application Information
AI Technical Summary
Problems solved by technology
Method used
Image
Examples
Embodiment 1
[0026] The main components of sulfuric acid slag raw materials are as follows:
[0027] Fe: 43.87%, S: 2.57%, As: 0.41%, Zn: 1.71%, SiO 2 : 20%, the rest is clay and impurities.
[0028] A, the above-mentioned sulfuric acid slag raw material is added water and screened with the conventional vibrating screen of the prior art, so that the fine matter falls through the mesh of the screen as much as possible, and the mass concentration under the screen is 12% ore pulp and the particulate matter on the screen, Particulate recycling;
[0029] B, by adding the amount of 32 grams of treating agent per ton of sulfuric acid slag raw material, add the treating agent made up of the raw materials of the following mass percentages in the slurry obtained in step A, and stir for 10 minutes:
[0030] Sodium Lauryl Sulfate 50%
[0031] Ammonium sulfate 50%;
[0032] C, after carrying out magnetic separation with the conventional magnetic separator of the prior art with the ore pulp that B s...
Embodiment 2
[0037] The main components of sulfuric acid slag raw materials are as follows:
[0038] Fe: 48.19%, S: 1.18%, As: 0.47%, SiO 2 : 18%, the rest is clay and impurities.
[0039] A, the above-mentioned sulfuric acid slag raw material is added with water and screened with the conventional vibrating screen of the prior art, so that the fine matter falls through the mesh of the screen as much as possible, and the mass concentration under the screen is 20% ore pulp and the particulate matter on the screen, Particulate recycling;
[0040] B, by the amount of adding 80 grams of treatment agent per ton of sulfuric acid slag raw material, add the treatment agent made up of the raw materials of the following mass percentages in the slurry obtained in step A, and stir for 5 minutes:
[0041] Sodium Lauryl Sulfate 80%
[0042] Ammonium sulfate 20%;
[0043] C, after carrying out magnetic separation with the conventional magnetic separator of the prior art with the ore pulp that B step h...
Embodiment 3
[0048] The main components of sulfuric acid slag raw materials are as follows:
[0049] Fe: 46.77%, S: 1.85%, As: 0.45%, Zn: 1.87%, SiO 2 : 21%, the rest is clay and impurities.
[0050] A, the above-mentioned sulfuric acid slag raw material is added water and is screened with the conventional drum sieve of prior art, and fine thing is dropped through the mesh hole of screen cloth as far as possible, and the mass concentration that obtains under the screen is the ore pulp of 16% and the particulate matter on the screen, Particulate recycling;
[0051] B, according to the amount of adding 50 grams of treatment agent per ton of sulfuric acid slag raw material, add the treatment agent made up of the raw materials of the following mass percentages in the slurry obtained in step A, and stir for 8 minutes:
[0052] Sodium Fatty Acid 62%
[0053] Ammonium sulfate 38%;
[0054] C, after carrying out magnetic separation with the conventional magnetic separator of the prior art with...
PUM
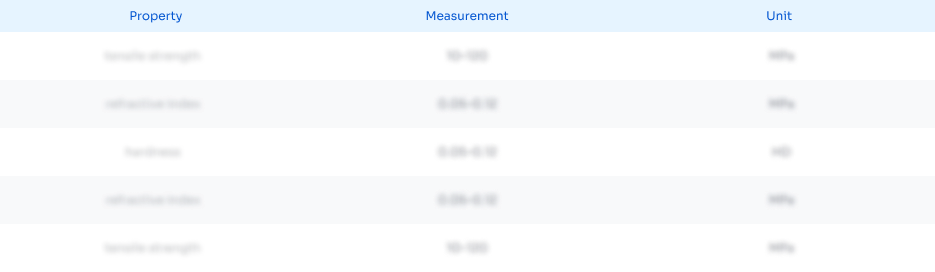
Abstract
Description
Claims
Application Information

- R&D Engineer
- R&D Manager
- IP Professional
- Industry Leading Data Capabilities
- Powerful AI technology
- Patent DNA Extraction
Browse by: Latest US Patents, China's latest patents, Technical Efficacy Thesaurus, Application Domain, Technology Topic, Popular Technical Reports.
© 2024 PatSnap. All rights reserved.Legal|Privacy policy|Modern Slavery Act Transparency Statement|Sitemap|About US| Contact US: help@patsnap.com