Method for preparing water soluble epoxy insulated resin in alkaline medium
A technology of epoxy insulation and alkaline medium, which is applied in the field of electrical insulation treatment. It can solve the problems of irregular shape particle size distribution, large particle size of dispersed phase, and inability to perform thick layer curing. The effect of low content and high stability of the solution
- Summary
- Abstract
- Description
- Claims
- Application Information
AI Technical Summary
Problems solved by technology
Method used
Examples
Embodiment 1
[0019] The first step: Weigh 10 parts by weight of epoxy resin E-12 (produced by Wuxi Resin Factory), 7 parts by weight of acetic acid, 2 parts by weight of succinic anhydride, 10 parts by weight of ethylene glycol, 2 parts by weight of methylamine and a conductivity of 10 μs 60 parts by weight of deionized water;
[0020] The second step: add epoxy resin, acetic acid, 20% succinic anhydride and 80% ethylene glycol in a 1000ml three-necked flask equipped with a stirrer, condenser, and dropping funnel, pass into nitrogen protection, and stir at 200 ° C React for 2 hours; add 70% succinic anhydride and the remaining ethylene glycol, stir and react at 160°C for 4 hours, add the remaining succinic anhydride, continue to keep warm for 1 hour, cool down to 110°C, add ether solvent, keep stirring for 0.5 h, add methylamine dropwise at 90°C, continue to heat and stir for 0.5 hours after adding, add deionized water, continue to heat and stir for 1 hour, and cool to room temperature to ...
Embodiment 2
[0022] The first step: take by weighing 25 parts by weight of epoxy resin E-20 (produced by Wuxi Resin Factory), 15 parts by weight of propionic acid, 8 parts by weight of maleic anhydride, 25 parts by weight of propylene glycol, 7 parts by weight of cycloethylamine, ethanol 15 parts by weight of glycol monomethyl ether and 30 parts by weight of deionized water with a conductivity of 0.1 μs;
[0023] The second step: add epoxy resin, propionic acid, 80% maleic anhydride and 20% propylene glycol in the 1000ml there-necked flask equipped with agitator, condenser, dropping funnel, pass into nitrogen protection, at 220 Stir the reaction at ℃ for 4 hours; add 10% maleic anhydride and the remaining propylene glycol, stir and react at 170°C for 7 hours, add the remaining maleic anhydride, continue the heat preservation reaction for 2 hours, cool down to 125°C, add ethylene Glycol monomethyl ether, heat preservation and stirring for 1 hour, add cycloethylamine dropwise at 100°C, conti...
Embodiment 3
[0025] The first step: take by weighing 17 parts by weight of epoxy resin E-44 (produced by Wuxi Resin Factory), 10 parts by weight of stearic acid, 5 parts by weight of phthalic anhydride, 17 parts by weight of diethylene glycol, 5 parts by weight of propylamine, 7.5 parts by weight of propylene glycol methyl ether and 30 to 60 parts by weight of deionized water with a conductivity of 1 μs;
[0026] The second step: add epoxy resin, stearic acid, 30% phthalic anhydride and 50% diethylene glycol in a 1000ml three-necked flask equipped with a stirrer, condenser, and dropping funnel, and pass into nitrogen protection , stirred and reacted at 210°C for 3 hours; added 70% phthalic anhydride and the remaining diethylene glycol, stirred and reacted at 165°C for 5 hours, added the remaining phthalic anhydride, continued the heat preservation reaction for 1.5 hours, and cooled to 120°C, add propylene glycol methyl ether, keep stirring for 0.5h, add propylamine dropwise at 95°C, contin...
PUM
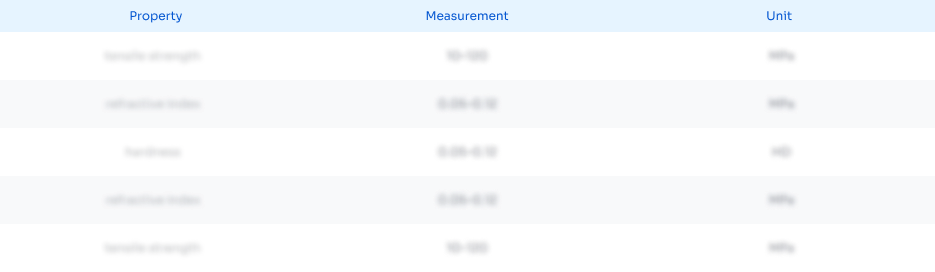
Abstract
Description
Claims
Application Information

- R&D Engineer
- R&D Manager
- IP Professional
- Industry Leading Data Capabilities
- Powerful AI technology
- Patent DNA Extraction
Browse by: Latest US Patents, China's latest patents, Technical Efficacy Thesaurus, Application Domain, Technology Topic, Popular Technical Reports.
© 2024 PatSnap. All rights reserved.Legal|Privacy policy|Modern Slavery Act Transparency Statement|Sitemap|About US| Contact US: help@patsnap.com