Method for preparing composite inorganic metal oxide
A technology of inorganic metals and oxides, which is applied in the field of preparation of composite metal oxides, can solve problems such as health hazards, and achieve the effect of being suitable for industrial production, with low toxicity and volatility
- Summary
- Abstract
- Description
- Claims
- Application Information
AI Technical Summary
Problems solved by technology
Method used
Image
Examples
Embodiment 1
[0025] 1) Under stirring conditions, add 8.986g of barium acetate into 100ml of glycerol, and heat to 200°C to completely dissolve the barium acetate;
[0026] 2) Add 10.000g of titanium isopropoxide under stirring condition;
[0027] 3) Reflux for two hours and then cool to room temperature to obtain a homogeneous liquid precursor;
[0028] 4) Calcining the homogeneous liquid obtained in the step 3) at 450°C, 500°C, 550°C, 700°C, 900°C or 1100°C respectively, and keeping it warm for 3 hours to obtain a powder.
[0029] figure 1 is the XRD pattern of the powder obtained by calcination of the precursor at different temperatures. It can be clearly seen from the figure that when the calcination temperature is greater than 550°C, the cubic barium titanate begins to form, and as the temperature increases, the cubic barium titanate gradually turns into the tetragonal barium titanate.
[0030] figure 2 It is the SEM image of the barium titanate powder prepared by calcination of ...
Embodiment 2
[0032] Comparative test a:
[0033] 1) Add 12.567g of barium acetate into more than 50ml of ethanol, ethylene glycol or 1,3-propanediol under stirring conditions, and heat to 200°C;
[0034] 2) Add 14.000g titanium isopropoxide under stirring condition;
[0035] 3) After reflux for two hours, it was cooled to room temperature, and it was observed that a homogeneous system could not be formed.
[0036] Comparative test b:
[0037] 1) Add 12.567g of barium acetate into more than 50ml of glycerol under stirring conditions, and heat to 200°C;
[0038] 2) Add 14.000g titanium isopropoxide under stirring condition;
[0039] 4) Reflux for two hours and cool to room temperature to obtain a homogeneous liquid.
Embodiment 3
[0041] 1) Mix 50ml of glycerol and 50ml of ethylene glycol to obtain a solution;
[0042] 2) Add 7.054g of barium acetate under stirring condition, and heat to 200°C to completely dissolve the barium acetate;
[0043] 3) Add 10.000g of n-butoxytitanium under stirring condition;
[0044] 4) Reflux for two hours and then cool to room temperature to obtain a uniform and stable liquid precursor;
[0045] 5) Calcining the precursor at 700° C. for 3 hours to prepare white barium titanate powder.
PUM
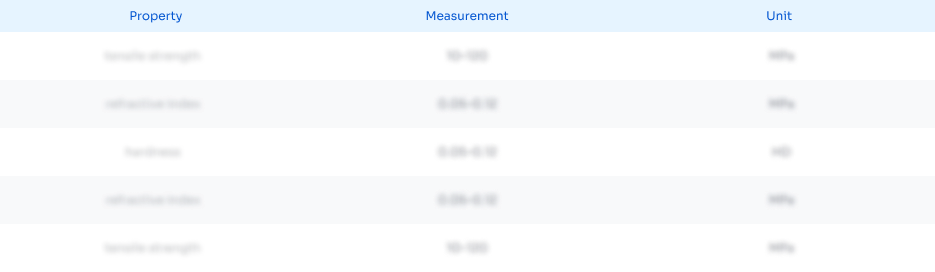
Abstract
Description
Claims
Application Information

- R&D
- Intellectual Property
- Life Sciences
- Materials
- Tech Scout
- Unparalleled Data Quality
- Higher Quality Content
- 60% Fewer Hallucinations
Browse by: Latest US Patents, China's latest patents, Technical Efficacy Thesaurus, Application Domain, Technology Topic, Popular Technical Reports.
© 2025 PatSnap. All rights reserved.Legal|Privacy policy|Modern Slavery Act Transparency Statement|Sitemap|About US| Contact US: help@patsnap.com