A mineral wool boiling melting method of directly using grainy waste slag and coal
A mineral wool and granular technology, which is applied in the field of low-pollution mineral wool boiling smelting, can solve the problems of difficulty in forming and curing mineral wool products, rising energy prices and transportation costs, and rising raw material costs for mineral wool smelting. The effect of taking materials, improving fiber formation rate and reducing transportation cost
- Summary
- Abstract
- Description
- Claims
- Application Information
AI Technical Summary
Problems solved by technology
Method used
Image
Examples
Embodiment 1
[0025] One or several of powdery blast furnace slag, coal gangue, fly ash, steelmaking waste slag, and boiler cinder are used as mineral wool raw materials, continuously and quantitatively added to the melting pool of the fluidized furnace, and coal powder is used as fuel. Using high-pressure and high-temperature air (≥500°C) to inject fuel into the melt below the liquid level of the molten pool of the boiling furnace through the nozzle, so that the fuel burns violently inside the melt, and provides molten raw materials, auxiliary materials and other heat consumption to the molten pool At the same time as the necessary heat, the molten pool will be violently boiled, thereby accelerating the melting and homogenization of mineral wool raw materials. If necessary, control the number of strands within the required range, and then guide the strands to the material roller of the fiber-forming centrifuge to carry out the normal mineral wool fiber-forming process. Mineral wool fiber p...
Embodiment 2
[0028] Rebuild the original mineral wool cupola of the independent mineral wool production line with an annual output of 5,000-20,000 tons into a fluidized smelting furnace, add coal powder preparation and conveying system, raw material storage and conveying system, and high-temperature heating and air supply system. The smelting furnace together constitutes a new mineral wool smelting system. The powdered mineral wool raw material and coal powder are fully burned and reacted in the furnace to produce mineral wool melt. The size of the stream is controlled through the adjustable nozzle, and the melt stream is introduced into the centrifuge. Finally, the mineral wool melt is converted into fibrous mineral wool, and then it is connected with the original mineral wool production follow-up process. Through solidification, shaping, cooling, cutting, inspection and other processes, qualified mineral wool board products are produced. At the same time, the flue gas from the heat exchan...
Embodiment 3
[0031] Combining with ironmaking blast furnace or power plant cyclone furnace, utilizing the sensible heat of blast furnace slag or cyclone furnace liquid slag to carry out boiling smelting of mineral wool, can reduce smelting energy consumption more greatly (compared with embodiment 2). The specific method is: establish a mineral wool fluidized smelting furnace and a mineral wool product production line near the ironmaking blast furnace or the cyclone furnace of a power plant, and directly introduce high-temperature blast furnace slag or cyclone furnace liquid slag as the main raw material of mineral wool into the fluidized smelting furnace (not Use cold mineral wool as the main material), and then spray coal powder or other fuels into the melt to keep the auxiliary materials melting and other heat needs, and add auxiliary materials continuously and quantitatively to temper the melt, and chemically melt the melt The composition is adjusted to the range required by mineral wool...
PUM
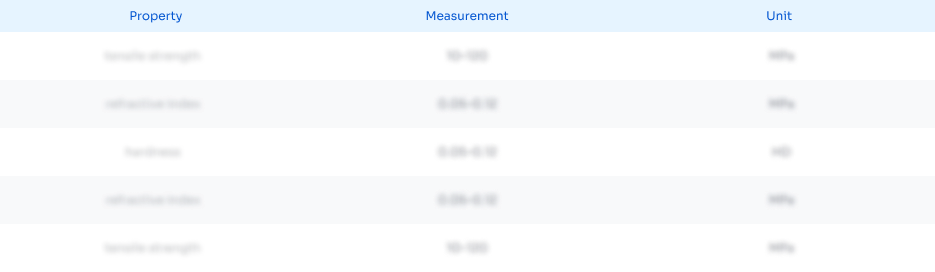
Abstract
Description
Claims
Application Information

- R&D
- Intellectual Property
- Life Sciences
- Materials
- Tech Scout
- Unparalleled Data Quality
- Higher Quality Content
- 60% Fewer Hallucinations
Browse by: Latest US Patents, China's latest patents, Technical Efficacy Thesaurus, Application Domain, Technology Topic, Popular Technical Reports.
© 2025 PatSnap. All rights reserved.Legal|Privacy policy|Modern Slavery Act Transparency Statement|Sitemap|About US| Contact US: help@patsnap.com