Copper alloy sheet and QFN package
A copper alloy plate and copper alloy technology, applied in electrical components, circuits, electrical solid devices, etc., can solve the problem of not being able to fully restrain the wire dragging burrs and blade wear, and achieve the effect of reducing blade wear and burrs.
- Summary
- Abstract
- Description
- Claims
- Application Information
AI Technical Summary
Problems solved by technology
Method used
Image
Examples
Embodiment 1
[0051] First, an embodiment of the first invention of the present invention is shown.
[0052] Copper alloys having the compositions No. 1 to 21 shown in Table 1 were melted under a charcoal coating in the air in a small electric furnace to melt an ingot with a thickness of 50 mm, a width of 80 mm, and a length of 180 mm. The front and back sides of the ingot were surface-cut by 5 mm each, and then hot-rolled at 950° C. to form a 12 mm-thick plate, and then the front and back sides of the plate were surface-cut by about 1 mm. In addition, since No. 20 had a large number of pores in the ingot, and No. 21 had hot rolling cracks, the steps after hot rolling were respectively stopped.
[0053] [Table 1] chemical composition (mass%, ** Standard: PPM), finishing processing rate (%)
[0054]
[0055] * The position of excess or deficiency.
[0056] These plate materials were annealed after cold rolling, and the plate thickness was adjusted to 0.15 mm by finish cold rolling. T...
Embodiment 2
[0081] Next, an embodiment of the second invention of the present invention is shown.
[0082] Copper alloys having compositions of No. 1 to 24 shown in Table 3 were melted under a charcoal coating in the air in a small electric furnace to melt an ingot with a thickness of 50 mm, a width of 80 mm, and a length of 180 mm. The front and back sides of the ingot were surface-cut by 5 mm each, and then hot-rolled at 950° C. to form a 12 mm-thick plate, and then the front and back sides of the plate were surface-cut by about 1 mm. In addition, since No. 23 had a large number of pores in the ingot, and No. 24 had hot rolling cracks, the steps after hot rolling were stopped.
[0083] [Table 3] chemical composition (mass%, ** Standard: PPM), finishing processing rate (%)
[0084]
[0085]
[0086] №18: Cu-Fe-P system * The position of excess or deficiency.
[0087] №19: Cu-Ni-Si system
[0088] These plate materials were annealed after cold rolling, then cold rolling and ann...
PUM
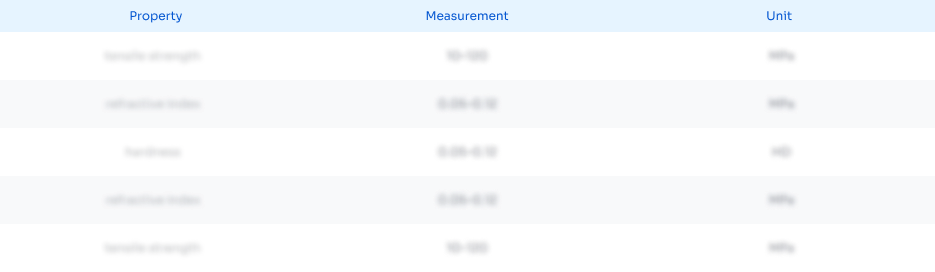
Abstract
Description
Claims
Application Information

- Generate Ideas
- Intellectual Property
- Life Sciences
- Materials
- Tech Scout
- Unparalleled Data Quality
- Higher Quality Content
- 60% Fewer Hallucinations
Browse by: Latest US Patents, China's latest patents, Technical Efficacy Thesaurus, Application Domain, Technology Topic, Popular Technical Reports.
© 2025 PatSnap. All rights reserved.Legal|Privacy policy|Modern Slavery Act Transparency Statement|Sitemap|About US| Contact US: help@patsnap.com